El VI Fórum Técnico de Tratamiento Térmico, TRATER DAY 2023, que esta edición ha retomado su formato presencial, ha reunido a empresas referentes del sector, así como una significativa representación de sectores estratégicos que aplican los tratamientos térmicos a sus productos.
En línea con los retos y los crecientes requerimientos de las industrias fabricantes y usuarias de componentes metálicos, el sector de los tratamientos térmicos se enfrenta al desafío de proponer e incorporar soluciones innovadoras y eficientes que permitan mejorar las características y la durabilidad de los materiales y los productos dirigidos a sectores altamente exigentes como son el aeronáutico, el naval o el de automoción.
Con el objetivo de compartir y dar a conocer algunas de las innovaciones de referencia para el sector, el INSTITUTO DE FUNDICIÓN TABIRA, el Centro de Investigación Metalúrgica AZTERLAN y TRATER PRESS celebraron el 17 de octubre el VI Fórum Técnico de Tratamiento Térmico, también conocido como TRATER DAY. En torno a una agenda de marcado carácter técnico, la organización del evento consiguió reunir a un significativo número de empresas y profesionales industriales en un encuentro que, tras dos años, ha vuelto a celebrarse en formato presencial.
El programa de la jornada contó con la colaboración de técnicos y especialistas de primer nivel de las empresas MONOCROM, ESI GROUP, GH INDUCTION GROUP, NIPPON GASES y OERLIKON BALZERS, así como del propio Centro Tecnológico AZTERLAN y de la ORGANIZACIÓN MUNDIAL DE FUNDICIÓN (WFO). El encuentro, esponsorizado por ESI GROUP, contó también con el apoyo de los organismos DEK Durangaldea Empresa Ekimena y EUSKALIT.
Tras una bienvenida por parte de los representantes del INSTITUTO DE FUNDICIÓN TABIRA y de AZTERLAN, representados consecutivamente por el Secretario General de I. F. Tabira, José Javier González, y por el Director General de AZTERLAN, el Dr. Garikoitz Artola, la sesión dio comienzo con una Key Note de la empresa fabricante de láseres MONOCROM, a cargo del Dr. Igor Alexander, Application Solution Manager de la compañía con sede en Barcelona. En su presentación Alexander abordó las ventajas que aporta el empleo de stacks de láseres de diodo a la tecnología de tratamiento térmico, destacando la “flexibilidad, modularidad y precisión que permiten los láseres de diodo en formato stack a las aplicaciones de calentamiento”.
La aproximación general se particularizó en varios casos de estudio aplicados a un espectro de sectores y temperaturas de calentamiento muy diverso, que reflejó la versatilidad de las aplicaciones de los láseres en los tratamientos térmicos. Entre las aplicaciones presentadas, destacaron las relacionadas con procesos de ablandamiento integrados en líneas de chapa, la generación de zonas de rótulas plásticas en componentes de crash, ya ensamblados en conjuntos complejos de chasis y los procesos de secado superficial y/o curado de pinturas. Dentro de esta casuística, el experto de MONOCROM expuso “la enorme ventaja de aprovechar las sinergias entre los sistemas de calentamiento convencionales y los sistemas láser adaptables”. Apuntaló esta afirmación presentando un caso de uso en el que la combinación de sistemas láser con control en lazo cerrado, instalados a la salida de un horno convectivo de resistencias, permitía ajustar pieza a pieza el final del proceso de curado aplicando potencia térmica de forma exclusiva en las zonas que lo necesitaran.
La presentación generó el interés de la audiencia, lo cual quedó patente en la participativa ronda de preguntas en la que se discutió, incluso, la aplicación de la tecnología láser para tratamiento de secciones gruesas.
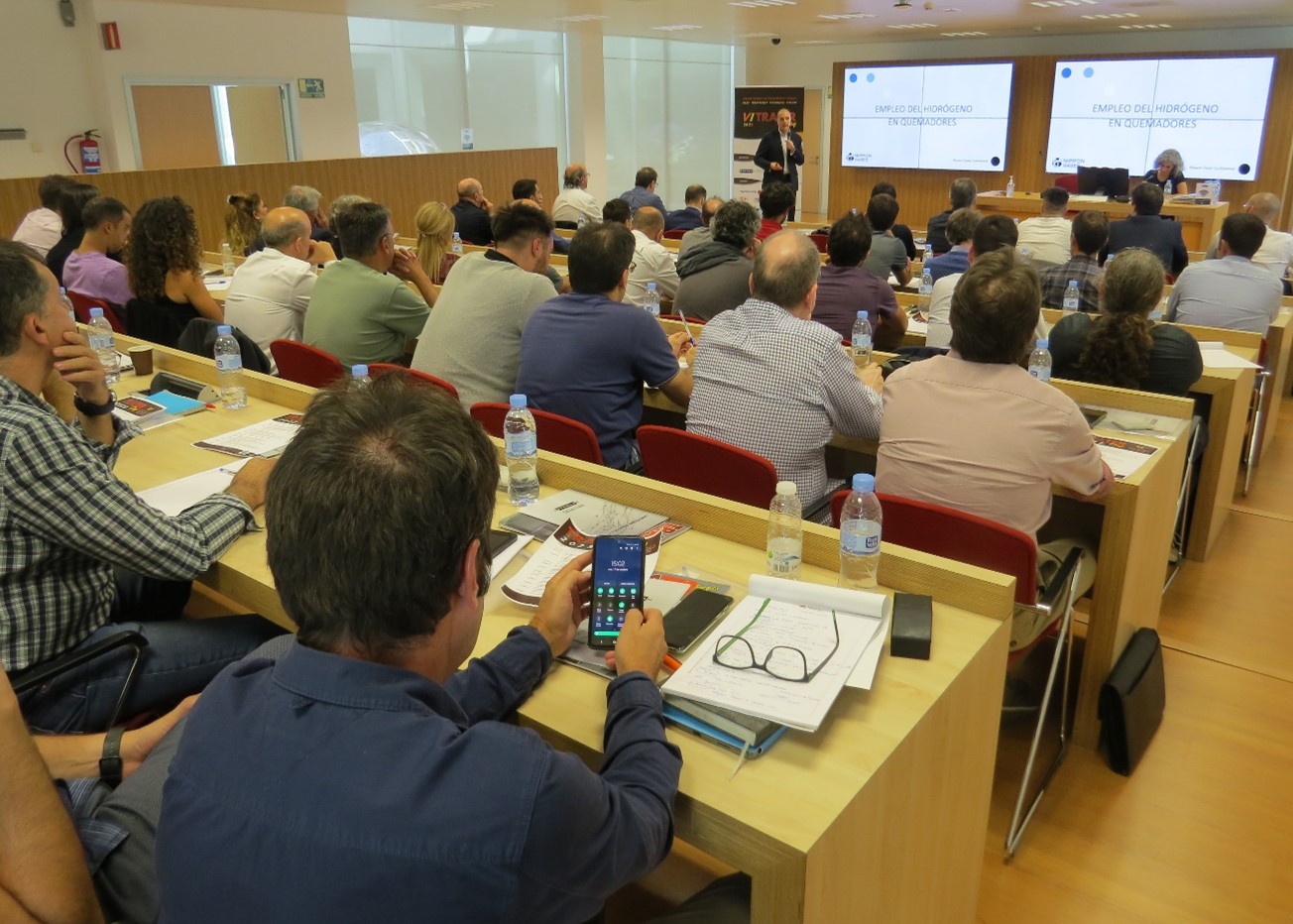
El encuentro generó el interés de expertos de la industria de tratamientos térmicos y su cadena de valor.
Siguiendo con otra tecnología de gran actualidad, como son las herramientas de simulación y predicción aplicadas al proceso de diseño y fabricación, Igor Pérez Villalobos de la empresa desarrolladora de software de simulación ESI GROUP presentó las capacidades y retos del tratamiento térmico virtual mediante el uso del software Sysweld, desarrollado por la compañía, destacando la eficiencia energética, la productividad y el aumento de control sobre el proceso.
En palabras del experto en simulación, la “eficiencia energética con el fin de disminuir las emisiones de CO2”. es uno de los principales retos industriales que aborda la simulación para analizar los efectos térmicos del tratamiento térmico, permitiendo realizar procesos de tratamiento térmico más eficientes y menos costosos a nivel energético.
Paralelamente, con el foco puesto en la productividad, el representante de ESI Group expuso cómo la simulación “ayuda a reducir los tiempos de ciclo y a realizar un prototipado virtual, sustituyendo ensayos físicos reales por virtuales y permitiendo realizar distintos diseños con el objeto de minimizar los ciclos térmicos que, además, ayudan a reducir los costos operacionales”. En esta misma línea, y ligado a la creciente incorporación de tecnologías de automatización, digitalización y control de los procesos industriales, Pérez Villalobos recalcó las oportunidades que ofrece esta tecnología. “Combinada con tecnologías como los gemelos digitales y las tecnologías de control de proceso, la simulación de tratamientos térmicos permite realizar una simulación predictiva e incluso una simulación en tiempo real dirigida a facilitar la toma de decisiones”.
La integración de la simulación de los tratamientos térmicos con otras fases del proceso de fabricación fue otro de los puntos fuertes destacados en la presentación de ESI Group. “No podemos obviar que los tratamientos térmicos son postprocesos que vienen a continuación de otros procesos de transformación, como la forja, la estampación o la fundición. Las tecnologías de simulación permiten concatenar los análisis del proceso de fabricación junto con el posterior tratamiento térmico”.
Finalizando su exposición, el experto de ESI Group ilustró las diferentes aplicaciones de la simulación aplicada a los tratamientos térmicos a través de varios casos de estudio y recalcó la importancia del ecosistema conformado por desarrolladores de software, centros tecnológicos y centros de enseñanza como elementos tractores y facilitadores fundamentales para incorporar los tratamientos térmicos en la industria.
La siguiente ponencia, a cargo de Sergio Forner García, Sales Area Manager (Spain and Portugal) de GH INDUCTION GROUP, se enfocó en las tecnologías de digitalización y fabricación aditiva. En su intervención, Forner también destacó la importancia de las herramientas de simulación para adaptarse a las nuevas demandas industriales y mejorar la eficiencia de los procesos propiciando el “ahorro en costes de energía, horas de trabajo y desperdicios de material”.
Como novedad tecnológica, el representante de la empresa fabricante de hornos industriales dio a conocer la tecnología patentada por GH para fabricar bobinas mediante el proceso de fabricación EBM (Electron Beam Melting). En este caso, “se trata de un proceso de fabricación aditiva que se realiza en una atmosfera controlada, a una temperatura elevada y se realiza capa por capa”. Forner tildó esta tecnología de fabricación 3D como revolucionaria, por las importantes ventajas que ofrece en cuanto capacidad para desarrollar formas complejas, reducir el peso de las bobinas y ahorrar costes.
Al igual que en la ponencia anterior, Forner también resaltó las sinergias de la concatenación de tecnologías: “el empleo combinado de simulación de procesos de inducción e impresión por EBM de los inductores utilizados en las pruebas simuladas, ha permitido reducir el número de iteraciones de desarrollo de los sistemas de inducción por un factor de tres a uno”.
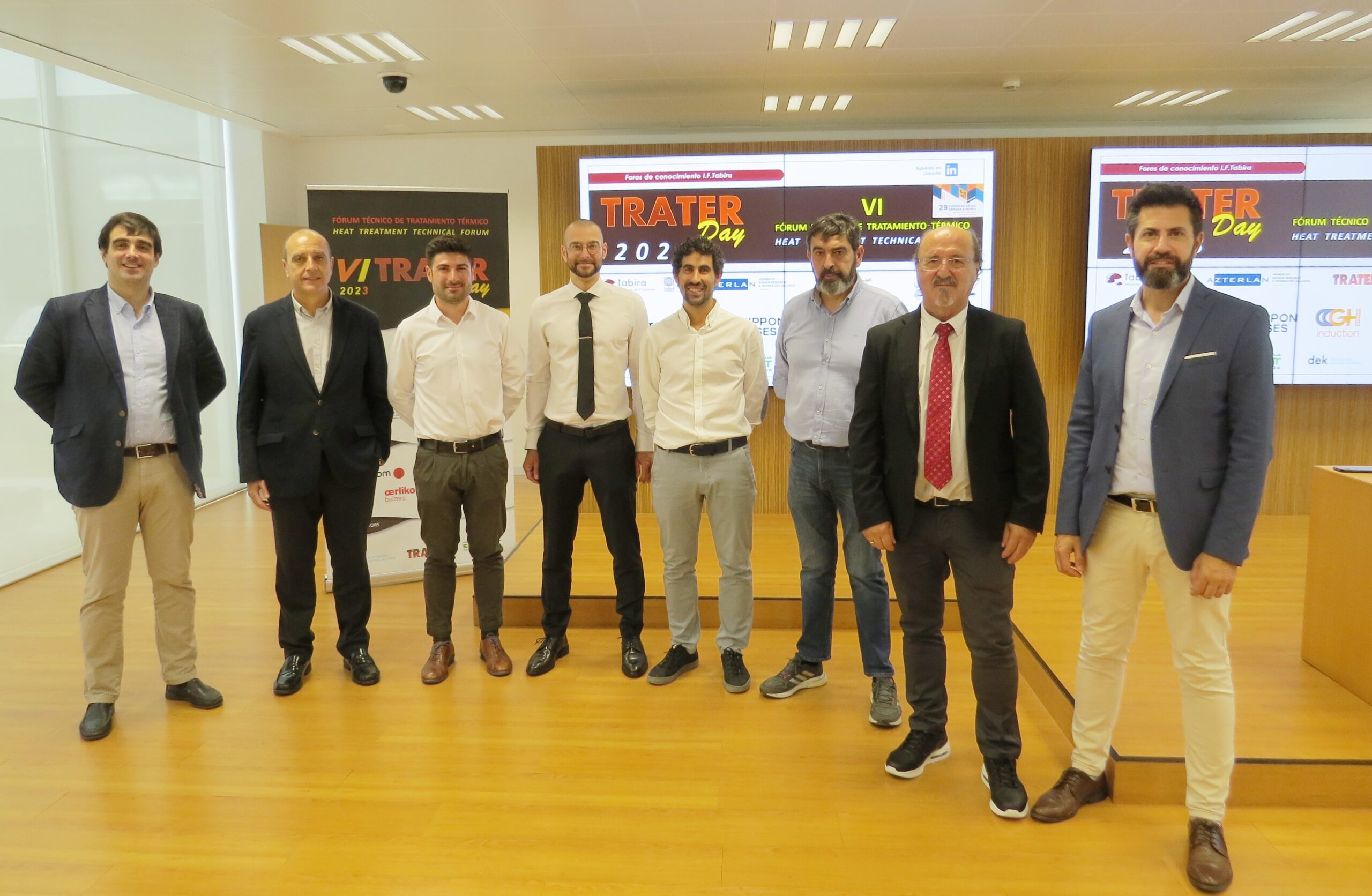
El equipo de ponentes y colaboradores de este Fórum Técnico de Tratamiento Térmico.
La última ponencia de la mañana corrió a cargo del Responsable de Tecnologías de Fundición de Hierro de AZTERLAN, Aitor Loizaga, quien compartió una ponencia en torno al aprovechamiento del calor residual acumulado en componentes de hierro tras la colada y utilizarlo para realizar un tratamiento térmico de la familia de los temples bainíticos, sin aportes energéticos externos.
Tal y como explicó Loizaga, “el aprovechamiento del calor residual debe realizarse de forma muy controlada y requiere adecuar la composición química del metal de partida”. En este sentido, Loizaga presentó los perfiles de enfriamiento adecuados para conseguir grados de fundición bainítica, también conocidos como ADI (Austempred Ductile Iron). Expuso cómo, con el know-how apropiado, es posible diseñar la composición química y la secuencia de desmoldeo y mantenimiento en medio aislante que permite conseguir propiedades homogéneas, incluso en componentes que presentan cambios de sección relevantes.
El experto en fundición indicó que AZTERLAN lleva más de diez años desarrollando este tipo de tratamientos y materiales de altas prestaciones, y remarcó que, aunque el concepto es sencillo, su aplicación no es directa, existiendo aún barreras técnicas para su empleo en empresas de fundición ya instaladas. “No todas las líneas de moldeo permiten acceder a los moldes que se desea procesar en el momento en el que el componente se encuentra a la temperatura adecuada”. No obstante, Loizaga aseguró que los beneficios que ofrece el tratamiento ADI en línea, en términos de costes y plazos de entrega, justifican seguir investigando y desarrollando este ámbito.
La sesión de tarde de TRATER DAY 2023 abordó la conexión del tratamiento térmico con la reducción de huella de carbono en la industria, discusión en la que se contó con la visión de la WFO (Organización Mundial de Fundición – World Foundry Organization) a través de su Secretario General, José Javier González.
Contextualizando el desafío, González indicó que “el mensaje de que hay que reducir las emisiones de gases de efecto invernadero es inequívoco. En conjunto, los acuerdos vigentes han generado una presión cada vez mayor a favor de la descarbonización en todos los sectores industriales”. En sus palabras, para avanzar en ese desafío parece necesario estudiar de un modo sistemático la relación entre la estructura energética y las emisiones de CO2 dentro de la industria. “La reducción total de CO2 depende de la intensidad de carbono de la electricidad suministrada. Esto significa que una de las premisas para hacer más ecológica la industria siderúrgica es la descarbonización del sector eléctrico”.
Según expuso, entre el 20% y el 50% de los aportes energéticos industriales se pierden en forma de calor residual e indicó que factores como la cantidad y temperatura de calor y la disponibilidad de un uso final viable son claves relacionadas con las contribuciones del tratamiento térmico a la descarbonización. Así, el secretario general de la WFO señaló que “el tratamiento térmico ofrece grandes oportunidades como fuente y como uso del calor residual. Como fuente, se pueden utilizar los gases de escape del proceso y el calor de las propias piezas. Como uso, los hornos de recocido y revenido a baja temperatura pueden beneficiarse de los flujos de calor residuales”.
Dentro de todos los escenarios posibles en los que la adopción de medidas de eficiencia energética se superpone con el reciclaje de materiales y otras innovaciones, destacó que el hidrógeno puede jugar un papel importante en la consecución de los objetivos de descarbonización industrial, si bien “es actualmente una innovación con un alto grado de incertidumbre y riesgo por los desafíos que supone, aunque se está trabajando intensamente en ello”.
Conectando esta preocupación mundial por reducir las emisiones de CO2 a la atmósfera, Jorge Visús (Combustion & Heat Treatings Market Manager de NIPPON GASES España, S.L.U.) abordó de forma más específica los retos del hidrógeno como combustible.
Tal y como reforzó Visús, el H2 se establece como una posible futura fuente de energía. La Comisión Europea se encuentra promoviendo el uso de H2 en la industria y, a corto plazo, se plantea la utilización de mezclas de gas natural e hidrógeno como combustible. Ante este reto tecnológico, el experto en gases recalcó que “urge desarrollar quemadores capaces de trabajar con mezclas de Gas Natural e Hidrógeno, e incluso con 100% H2”. El ahorro de energía con quemadores de oxicombustión se destacó también como un aspecto importante, donde según el experto “la combustión con oxígeno ahorra gran cantidad de combustible en los procesos de calentamiento, mayor cuanta más temperatura de salida tengan los humos”.
En cuanto a los retos de la utilización de hidrógeno como combustible, que en la mencionada conversación con el responsable de la WFO ya se apuntaba como muy relevante para alcanzar los retos de la descarbonización industrial en Europa, el responsable de Nippon Gases identificó “el desarrollo de quemadores que permitan utilizar 100% GN, 100% H2 y cualquier porcentaje de mezcla de ambos combustibles”, así como el aumento de la temperatura de llama, el cambio en la composición de los humos, la logística de suministro del Hidrógeno y el coste.
Seguidamente, y cambiando de tercio en cuanto a tecnología, OERLIKON BALZERS COATING SPAIN representada por su Sales Manager Juan Carlos Cengotitabengoa presentó las últimas innovaciones en soluciones de superficie desarrolladas por la compañía, los recubrimientos PVD (Physical Vapour Deposition). Según sus palabras, estos recubrimientos han presentado un gran avance en los últimos años, ofreciendo significativas características y permitiendo conseguir mayores espesores de recubrimiento. “PVD significa deposición física de vapor. Para lograr este acabado PVD, se realiza un proceso que se lleva a cabo en alto vacío y, en la mayoría de los casos, a temperaturas de entre 150 y 500 °C”.
Entre los recubrimientos PVD presentados por el representante de OERLIKON BALZERS destacan los recubrimientos de carbono que proporcionan una dureza excepcional 60-70 GPa, alta resistencia al desgaste y espesor muy fino. Estos recubrimientos están especialmente pensados para dar respuesta a las demandas de los procesos de transformación de aluminio, cuyo creciente peso en el vehículo eléctrico está sirviendo de acicate para acometer nuevos desarrollos también en el ámbito de la PVD.
El cierre de la jornada vino de la mano del Dr. Garikoitz Artola, Director General del centro tecnológico AZTERLAN, quien presentó una nueva aproximación experimental al estudio del impacto de las variables de tratamiento térmico sobre las propiedades de las aleaciones a través de un caso práctico. Más concretamente, esta segunda ponencia de AZTERLAN se centró en las baterías de ensayos de alto rendimiento, que permiten testear un número elevado de condiciones de proceso minimizando la inversión de recursos necesarios para este fin.
En palabras de Artola “consideramos que este nuevo método es tan prometedor que estamos en proceso de publicarlo en detalle en una revista científica de alto impacto para beneficio de la comunidad de investigación”. Así, la ponencia permitió adelantar al público presente en la jornada estas novedosas prácticas de laboratorio que todavía no han sido publicadas en acceso abierto.
La propuesta presentada por el experto de AZTERLAN consiste en una combinación de los ensayos Jominy con la técnica de Small Punch Testing, que en el caso que sirvió de hilo conductor para la ponencia, demostró reducir hasta en un orden de magnitud los recursos empleados para estudiar el impacto de las condiciones de tratamiento de temple y revenido sobre las propiedades mecánicas de los aceros. Sin embargo, también apuntó que “existen mejoras en las capacidades de ensayo, ya que uno de los grandes beneficios, más allá de la productividad alcanzada, es la resolución obtenida en las velocidades de temple. Somos capaces de discriminar variaciones muy pequeñas en la velocidad de enfriamiento”.
Los resultados presentados en el encuentro ya han comenzado a emplearse en casos industriales a pesar de que forman parte de una tesis doctoral aún en curso, desarrollada por Ibon Miguel, investigador de AZTERLAN, bajo la codirección del propio Artola.
A modo de conclusiones, los organizadores del evento destacan que esta última edición del Fórum Técnico de Tratamiento Térmico refuerza la necesidad y el interés del sector por seguir apostando por la innovación, siendo consciente del rol crítico que juega en la producción de componentes metálicos de alta exigencia. Contar con puntos de encuentro presenciales que permitan compartir y discutir preocupaciones, tendencias y retos tecnológicos para seguir mejorando su competitividad y su aportación de valor añadido a su cadena de valor es un aspecto clave. “Tras un período fuertemente marcado por la pandemia, en el que solo habíamos podido celebrar este encuentro en-línea, hemos podido ver que, además del contenido técnico, el sector ha respondido positivamente a la idea de volver a reunirse y compartir y debatir en persona”.