La conferencia Druckgusstag se celebra en el seno de la conocida feria Euroguss dedicada a las tecnologías de inyección de aluminio. En este destacado encuentro técnico internacional, AZTERLAN ha presentado el desarrollo de la tecnología Alu-V® de aplicación en el proceso HPDC y la integración avanzada de sensores mediante tecnologías aditivas en moldes de inyección.
En la primera de las ponencias el investigador de Materiales Ligeros del Centro de Investigación Metalúrgica AZTERLAN Sergio Orden, ha dado a conocer uno de los últimos desarrollos del Centro para la fundición inyectada: la tecnología Alu-V®, capaz de generar bajo-medio vacío, y Alu-V+, sistema de generación de alto vacío. “Las porosidades provocadas por el aire retenido en los moldes son un problema inherente a la fabricación por el proceso HPDC. Cuando el metal líquido se inyecta a tan alta velocidad en el molde, el aire en su interior no dispone de salidas suficientes para ser extraído y parte del mismo es atrapado en el metal, generando porosidad de gases. Con el desarrollo de la tecnología Alu-V® (y Alu-V+) hemos querido reducir este riesgo y asegurar una mayor calidad en los componentes de aluminio inyectados”. Si bien existen en el mercado otras herramientas de generación de vacío, “estas otras soluciones presentan importantes limitaciones, dada su tendencia a generar un efecto de succión que provoca un patrón de llenado inconsistente de los moldes, afectando a la calidad de las piezas”.
En palabras de Sergio, la generación de vacío mediante este nuevo desarrollo aporta significativas oportunidades de proceso, como, por ejemplo, “el desarrollo de componentes con paredes más finas o el aseguramiento de la soldabilidad o la tratabilidad térmica de las piezas”. Asimismo, “hemos creado Alu-V+ (alto vacío) con el fin de facilitar la fabricación de componentes estructurales y de mayor responsabilidad”.
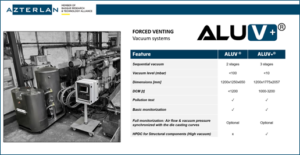
Alu-V® Druckgusstag presentation
El representante de AZTERLAN recalcó en su intervención la importancia de las tecnologías de industria 4.0 y la monitorización de parámetros clave del proceso para asegurar la efectividad del mismo y la calidad del resultado. En este sentido, afirmó que “en el desarrollo de las tecnologías Alu-V® hemos tenido en cuenta las crecientes necesidades de control de proceso de la fundición inyectada, por lo que hemos asegurado que nuestros equipos son capaces de capturar y emitir datos clave como presión, humedad y flujo de aire, sincronizados con el resto variables de inyección”.
Por otro lado, centrando su presentación en las oportunidades que las tecnologías de fabricación aditiva presentan para la fundición inyectada, el también investigador de la línea de Materiales Ligeros de AZTERLAN Emili Barbarias presentó dos experiencias exitosas ligadas a la optimización y monitorización de este proceso, desarrolladas junto las empresas VOESTALPINE y ELECTRONICS GmbH.
La primera de las experiencias compartidas por el investigador de Azterlan consiste en un innovador distribuidor ubicado en la cámara fría de HPDC desarrollado mediante tecnologías aditivas, cuya implantación ha permitido “reducir el tiempo de ciclo en 3 segundos respecto a distribuidores convencionales. La principal razón es una significativa mejora en la capacidad para disipar el calor”. Como explicó Emili, esta experiencia ha ido acompañada de la integración de varios sensores (termopares y un sensor de temperatura de la cavidad en contacto con el metal), que han permitido al equipo de trabajo monitorizar las variables clave y determinar el éxito de la invención.
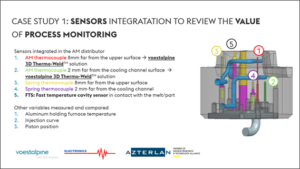
Inserto fabricado por tecnologías aditivas para HPDC
Como segunda experiencia de éxito llevada por el equipo de trabajo al Druckgusstag, el investigador de AZTERLAN presentó un rediseño optimizado de los canales de enfriamiento del sistema para mejorar la vida útil de un inserto sensorizado, fabricado también mediante tecnologías aditivas. “Se trata de un inserto que ofrece importantes datos relacionados con el rechupe y el die-soldering que, sin embargo, sufría un rápido deterioro y disponía de una baja vida por las altas tensiones que sufría. El objetivo de la mejora presentada consistió en prolongar su vida útil además de asegurar la estabilidad del proceso respecto a las incidencias en el molde y la calidad del producto. Actualmente estamos recogiendo numerosos datos críticos de proceso que nos proporcionarán una importante información y conocimiento en el futuro”. En la producción por HPDC es “habitual que los fenómenos que deseamos observar sucedan en zonas de difícil acceso del proceso de fabricación (como el interior de los moldes) donde las condiciones de trabajo son duras y afectan a la durabilidad de transductores y emisores de datos. Parte de nuestros esfuerzos de investigación en el ámbito de la industria 4.0 se orientan a asegurar que los parámetros críticos de proceso pueden captarse y que las vías por las que podemos realizar dicha captura sean consistentes, fiables y estables”.