Los últimos avances tecnológicos han provocado una automatización y digitalización de las fábricas y los sistemas productivos. Un aspecto clave ha sido el Internet de las cosas (IoF – Internet of Things), a partir del cual se ha conseguido una intercomunicación continua e instantánea entre los distintos dispositivos, productos y sistemas necesarios para elaborar un producto. Los datos generados, una vez filtrados, tratados y convertidos en información útil, junto con programas inteligentes capaces de tomar decisiones, permiten controlar y supervisar el proceso de producción completo. De esta manera, las personas, las máquinas y los productos fabricados disponen de canales de comunicación propios, pudiendo interactuar el uno en el otro en tiempo real para optimizar la eficiencia del proceso.
Las fundiciones actuales distan mucho de aquellas en las que prácticamente todo el proceso era artesanal. Su alto nivel de automatización les permite adecuar los últimos desarrollos en sistemas ciber-físicos (CPS – Cyber Physical Systems) que aglutinan, tanto sensores y actuadores integrados, como digitalización de cantidades ingentes de datos y comunicaciones (ICT- Information and Communication Technologies), habilitando una interactuación entre las características del producto final y los dispositivos utilizados en su fabricación. La captación de los parámetros de producción apropiados y su tratamiento a partir de programas de inteligencia artificial permiten obtener las mejores condiciones de fabricación para cada pieza en concreto, detectar cualquier parámetro fuera del intervalo de especificación y corregir cualquier anomalía en el proceso para garantizar el cumplimiento de los requerimientos de los clientes.
Avanzando un paso más, la capacidad de autoaprendizaje progresivo de las máquinas y su ajuste automático a las necesidades productivas específicas de cada momento, permiten disponer de un proceso gobernado inteligentemente sin la actuación humana. Es lo que se ha denominado “smart process”, donde todos los parámetros son controlados en continuo, asegurando un proceso robusto, fiable y flexible, que puede adaptarse por sí mismo a cualquier variación de pieza, producto o proceso.
Los desarrollos de técnicas de control avanzadas para corregir las desviaciones inherentes a las máquinas y la implementación de nuevos criterios de diseño basados en el conocimiento intrínseco de los fenómenos que ocurren en cada etapa de la fabricación permiten obtener el denominado “smart product”, el cual no precisa de ninguna operación que no aporte valor añadido, ofreciendo un producto de alta calidad y de inmejorable aspecto final, lo que repercute en la rentabilidad y en la imagen de la empresa. Este tipo de productos únicamente pueden ser fabricados en la fundición del futuro.
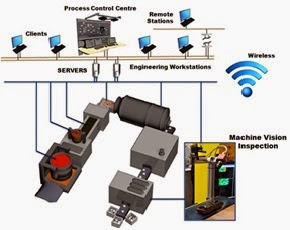
Esquema representativo de intercomunicación en un proceso productivo de fundición
IK4-Azterlan ha enfocado buena parte de los esfuerzos investigadores de los últimos años a desarrollar la tecnología necesaria para dar este salto. Adicionalmente a su reconocido sistema de control metalúrgico (Thermolan), los recientes desarrollos en programas de inteligencia artificial (Salomon), que permite obtener un mayor rendimiento a los parámetros recogidos en el proceso, y el software de simulación en tiempo real (Eidocalc), que incluye la calidad metalúrgica en dicho instante, permiten completar los sistemas de control necesarios para alcanzar el “smart process”.
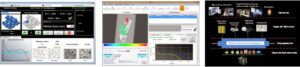
Tecnología desarrollada por IK4-Azterlan, que permite disponer de un “proceso inteligente” en fundición
Por otro lado, su amplia experiencia en el ajuste de las máquinas de moldeo, así como en la utilización de diseños innovadores permite la fabricación de piezas sin rebaba y cuyo sistema de alimentación se separa sin necesidad de operación alguna, lográndose el denominado “smart product”. De esta forma, el “lead time” existente entre la fusión de las materias primas y el producto final se reduce a un período de 5 horas en sistemas de producción con líneas de moldeo automáticas, debido a que únicamente es necesaria la inspección final y el embalaje.
Esta revolución es un hecho aunque todavía tiene retos pendientes. Tanto el “smart process” como el “smart product” deben combinarse con un IoT global. La implicación que tienen billones de sistemas y dispositivos capaces de comunicarse entre sí sin necesidad de intervención humana es enorme, ya que se dispondrá de toda la información de la cadena de valor de un producto del cual forma parte una pieza de fundición durante toda su vida útil. De esta manera se puede reaccionar de inmediato y de una manera más precisa ante cambios de tendencia y requerimientos de dicho mercado.
Adicionalmente, se generará información sobre fallos en servicio, los cuales, convenientemente analizados, permitirán conocer los aspectos que deben mejorarse en la fabricación, mecanizado, montaje, condiciones de funcionamiento, etc., para evitar disconformidades de los usuarios respecto a un determinado producto.
Este hecho, impensable hace unos años, será una realidad en un futuro no muy lejano, en el que el fabricante deberá hacer frente al análisis de cantidades ingentes de datos (Big Data) y el resto de partícipes, deberán adaptarse rápidamente a esta nueva metodología de trabajo, como es el caso de las fundiciones.