La familia de las superaleaciones la componen aquellas aleaciones cuyo elemento químico constitutivo fundamental es el Ni o el Co. Estos elementos junto con la adición de cantidades variables de otros elementos como el Cr, Nb, Ti, Al, Hf, Cu configuran un material con una elevada resistencia a la corrosión, a la deformación y a la rotura a elevadas temperaturas.
Esta combinación de características hace que su ámbito de aplicación se encuentre, principalmente, en motores de avión, turbinas para la generación de gas, o equipamiento para el transporte de gases o líquidos corrosivos a elevadas temperaturas.
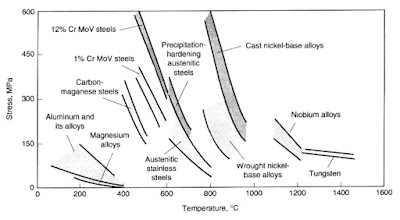
Figura 1: Carga de rotura de diferentes aleaciones en función de la temperatura (Fuente: “Heat Resistant Materials” – ASM INTERNATIONAL) |
Sin embargo, estas aleaciones de alto valor añadido son grandes desconocidas desde el punto de vista metalúrgico, quizás porque su mercado es mucho más limitado y también porque es limitada la investigación que sobre ellas se ha realizado hasta la fecha. Los procesos de fabricación de estas aleaciones son múltiples, siendo las piezas con solidificación direccional y las monocristal, las que están asociadas a los procesos más novedosos. En estos casos, la orientación y el tamaño del cristal formado son los aspectos fundamentales, que aportan propiedades muy específicas para usos muy concretos a los componentes fabricados con estos materiales.
No obstante, existe otra gama de piezas en el ámbito de las superaleaciones que trabajan a temperaturas inferiores, bajo esfuerzos puntuales, o con importantes requerimientos continuos en ambientes corrosivos muy agresivos. Algunas piezas creadas con estas aleaciones también tienen que ser soldadas para formar subconjuntos más complejos. En estos casos, sus procesos de fabricación se encuentran mayormente asociados a piezas fundidas, resultando en microestructuras de grano irregular y con un nivel de segregaciones verdaderamente significativo. Como consecuencia, se producen agrietamientos en los procesos de soldadura. Para paliar este efecto negativo, los diseñadores de componentes suelen optar por recurrir a diseños sobredimensionados en espesores y tanto fabricantes, como montadores, sufren dificultades para su recuperación.
Ante esta problemática, la solución lógica pasa por reducir el tamaño del grano y de las segregaciones, pero ponerla en práctica no resulta tan sencillo. Un primer acercamiento al problema lleva a pensar que con el uso de una arena más conductora y/o enfriadores localizados en los moldes, sería posible conseguir buenos resultados. Sin embargo, estas aleaciones tienen muy mala conductividad térmica y estas técnicas han demostrado unos resultados muy limitados.
Como consecuencia, el problema tiene que ser atacado desde dentro y, para ello, es necesario generar un efecto nucleante en estado líquido que, iniciado en el interior del metal, propicie la generación de una mayor cantidad de cristales y deje menos margen a la segregación de los elementos que constituyen la aleación.
Una de las oportunidades identificadas es el uso de inoculantes, productos químicos utilizados en algunas aleaciones, como la fundición de hierro, para la nucleación de algunas fases. El uso de inoculantes implica dos etapas fundamentales: la fabricación del inoculante en composición y granulometría adecuados y su posterior proceso de adición, teniendo en cuenta tanto la cantidad como el momento de realizar la inoculación, pues en función del tiempo transcurrido, puede producirse un efecto de desvanecimiento que limita dicho efecto inoculante. Los resultados de la inoculación son inequívocos y permiten reducir el tamaño de grano, sin que se observe la presencia de inclusiones en la muestra.
De forma similar al inoculante, pero basados en un subenfriamiento local (y no en la generación de partículas como núcleos de germinación), nos encontramos con los micro-chills. Mediante su adición en cantidad y composición adecuadas, se produce una germinación de núcleos de la misma aleación de forma local al enfriarse el área anexa por la fusión del núcleo introducido. Los resultados son similares al uso de la inoculación, pudiéndose observar el efecto en la reducción del tamaño de grano en una superaleación fabricada por cualquiera de los métodos anteriormente citados.

Figura 2: Imagen tamaño de grano en superaleación IN718 |
Con todo, estos no son los únicos métodos para modificar la microestructura de estas superaleaciones. Ayudados por modelizadores termodinámicos y termocinéticos se pueden simular procesos de disolución y precipitación de fases. Se trata de una representación gráfica de la evolución de las fases, que hace posible desarrollar tratamientos térmicos más eficaces para la obtener la mejor microestructura, en función de la etapa del proceso o condición de uso del componente que corresponda a la aplicación final del mismo.

Figura 3: Modelización de la formación y disolución de fases en un IN718 |
Sin duda, la modificación en la microestructura de superaleaciones fundidas por métodos tradicionales representa nuevas oportunidades de mejora, o potenciales nuevas aplicaciones para esta gama de materiales avanzados.