Esta tecnología, desarrollada con la finalidad de obtener componentes de inyección con alta ductilidad, excelentes propiedades mecánicas y un nivel muy reducido de porosidad, garantiza un nivel de defectos muy reducido en comparación con la tecnología convencional de inyección de aluminio. El componente inyectado puede ser tratado térmicamente obteniendo unas óptimas propiedades mecánicas, e incluso mejora su comportamiento a la soldabilidad.
En el sector de la automoción las piezas desarrolladas mediante tecnología VPDC se orientan fundamentalmente a cumplir una función estructural en los vehículos. Son piezas de seguridad con una gran capacidad de absorción de energía tras un impacto.
En cuanto al proceso, la tecnología VPDC comprende la aplicación de alto vacío en la cavidad del molde, tratamiento del metal (desgasificado, desescoriado, modificado del Si eutéctico, …), el uso de aleaciones primarias y, finalmente, un tratamiento térmico optimizado.
En la actualidad, existe entre las industrias de transformación metálica una importante presión/dedicación por mejorar la eficiencia de sus procesos, reduciendo su impacto ambiental y sus costes. Entre otras, una estrategia que va cogiendo fuerza es sustituir, al menos parcialmente, estas aleaciones primarias por aleaciones secundarias, recuperadas de residuos industriales o componentes fuera de uso.
Entre las tecnologías de moldeo de aluminio, se han desarrollado en efecto numerosas investigaciones y proyectos entorno a la sustitución de aleaciones primarias por aleaciones secundarias. Sin embargo, no existe apenas investigación para el empleo de aleaciones secundarias que obtengan una alta ductilidad en la tecnología VPDC/VHPDC.
Hoy en día, los componentes estructurales de automoción se fabrican en las aleaciones primarias del tipo AlSi10MgMn (ENAC 43.500) (registrada comercialmente como Silafont -36 (Rheinfelden), Aural-2, Aural-3 (Rio Tinto), Trimal 05 (Trimet), etc). Gracias a su elevado contenido de Mn (0,4%-0,8%), la aleación primaria AlSi10MgMn tiene un buen comportamiento al fenómeno “Die Soldering”. Un fenómeno que afecta negativamente a los procesos de transformación VPDC/VHPDC, incidiendo tanto sobre el componente fundido como sobre el molde, por quedarse parte del aluminio fundido pegado en este último. Si bien es cierto que una mayor presencia de Fe mejoraría incluso en un 20% más la vida del molde, este elemento representa la impureza más dañina para la obtención de propiedades mecánicas para las aleaciones de aluminio Al-Si.
Aunque, un mayor contenido de hierro es beneficioso para evitar el fenómeno Die Soldering, el Fe tiende a formar fases intermetálicas frágiles tales como β-Al5FeSi. Las fases β-Al5FeSi, de morfología placa/aguja, deterioran de forma significativa las propiedades mecánicas, especialmente, la ductilidad y la tenacidad a la fractura. En su lugar son preferibles las fases intermetálicas α-AlFeSi con morfología de escritura chinesca o poligonal.
«El fenómeno «Die Casting» afecta negativamente a los procesos de transformación VPDC/VHPDC, incidiendo tanto sobre el componente fundido como sobre el molde.»
Las empresas refinadoras, quienes comercializan las aleaciones secundarias tras la compra de chatarra de Aluminio, aseguran que su mayor problemática en obtener aleaciones secundarias próximas a la composición química de la aleación primaria AlSi10MgMn (ENAC 43.500) reside en los elementos Fe y Cu. El resto de las impurezas (como el Zn, Cr, Ni, Pb, etc.) no generan una problemática significativa.
Así, existen multitud de investigaciones dirigidas a mejorar las propiedades metálicas generales de las aleaciones Al-Si secundarias con alto contenido en Fe. Podrían clasificarse en cuatro los métodos que se han empleado para reducir las fases intermetálicas y frágiles β-Al5FeSi:
1) Controlar el contenido de Fe. Está basado en la selección de materias primas con muy bajo contenido de Fe. Generalmente, las aleaciones primarias Al-Si ofrecen un contenido de Fe entre 0,03-0,15%, siendo la media del mercado 0,07-0,10%. Sin embargo, en el mercado de las aleaciones secundarias se detectan diferentes niveles de contenidos de Fe, siendo el precio más barato cuanto mayor es el nivel de impureza.
2) Eliminación física del elemento del Fe sobre el metal. Este concepto relaciona la fusión “sudada” y la sedimentación de fases ricas de Fe, que posteriormente son extraídas del metal. Algunas investigaciones han tratado de eliminar el hierro de la aleación fundida de aluminio mediante filtración. El objetivo es precipitar fases intermetálicas ricas en Fe mediante la adición de Mn y reduciendo la temperatura de fusión. Sin embargo, esta técnica requiere elevados tiempos para la sedimentación e incluso implica una pérdida del 10% del Aluminio. Existe otra técnica mediante la agitación electromagnética para la separación de fases intermetálicas ricas en Fe del metal fundido, pero complica enormemente el proceso y es muy cara.
3) Interacción térmica sobre la aleación de aluminio. Este método está basado en dos tratamientos independientes.
- Over heating: Se trata de llevar a una elevada temperatura el metal para reducir la nucleación de los compuestos que forman las fases intermetálicas ß-Al5FeSi. La desventaja de este método es que, al aumentar la temperatura, existe un potencial riesgo de aumentar también el contenido de hidrógeno y óxidos en el metal. También se incrementa el tiempo y el coste del proceso.
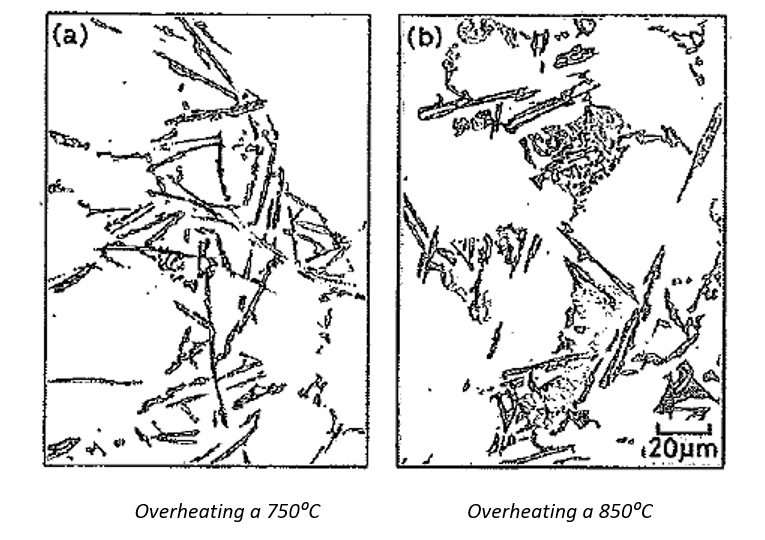
Figura 1. Microestructuras de la aleación AlSi6Fe0,4%con overheating a 750⁰C y a 850⁰C
- Incrementar la velocidad de solidificación: Tal como se ha descrito anteriormente, cuanto mayor es la velocidad de solidificación, las fases intermetálicas ß-Al5FeSi toman una menor longitud y menor espesor, e incluso se precipitan mayormente en fases intermetálicas α-AlFeSi si la velocidad de solidificación es elevada. Es un método muy empleado en la tecnología de moldeo en arena y coquilla, pero en la fundición inyectada no es aplicable ya que su velocidad de solidificación ya es bastante elevada.
4) Neutralización química de las fases intermetálicas ß-Al5FeSi. Esta neutralización se obtiene mediante las microadiciones de diferentes elementos como Mn, Cr, Sr, Be, V, Co, P, K y Be y las combinaciones de dos, o varios elementos. Se describe a continuación el efecto del Mn y el Cr y sus combinaciones.
- Por su parte, el Mn es ampliamente utilizado y su contenido está relacionado con el Fe según la siguiente regla Fe: %Mn>0,5 x Fe%. Pero la micro adición del Mn debe optimizarse ya que cuando consigue reducir casi hasta la totalidad las fases ß-Al5FeSi, las fases intermetálicas α-AlFeSi de morfología poligonal o estrella aumentan considerablemente su tamaño, decreciendo la ductilidad de la aleación.
- En cuanto al Cr, tiene un efecto similar que el Mn. En las investigaciones realizadas por la Universidad de Padova junto con la refinería Metalli Capra, en las aleaciones AlSi9Cu3 con un elevada velocidad de solidificación, como la de la fundición inyectada, la microadición de Cr junto una elevada velocidad de solidificación promueve la formación de compuestos Sludge primarios y fases intermetálicas proeutecticas α-Alx(Fe,Mn,Cr)ySiz y aumentan la fracción de área de las fases intermetálicas ricas en Fe en cuanto se incrementa el contenido de Cr en la aleación. La investigación de los coreanos Hyun You Kim, Sang Won Han and Hyuck Mo Lee también analizó la influencia de la combinación de Mn y Cr. Para un contenido de Fe de 0,2% en la aleación A356, con un contenido de Cr=0,13% y Mn=0,13% se obtenían fases intertermetálicas α-AlFeSi de menor tamaño que con únicamente la adición de Mn de 0,2%. Se justifica este hecho ya que el coeficiente de difusión del Cr es menor que el Mn. En otro trabajo realizado por el Centro Investigación Metalúrgica IK4-Azterlan se muestra cómo en la tecnología de moldeo en arena con la aleación AlSi7Mg0,3 con un contenido de Fe de 0,3% tras optimizar la microadición de los elementos Mn, Cr y V se obtienen el mismo índice de calidad que con una aleación primaria de AlSi7Mg0,3 con un contenido de Fe de 0,09%. E incluso también se remarca que, incrementando el contenido de Mn, Cr y V por encima del contenido óptimo, las fases intermetálicas ricas en Fe aumentan tanto en tamaño como en fracción de área empeorando las propiedades mecánicas. Se muestra a continuación en la figura 10 la transformación de las fases intermetálicas ß-Al5FeSi a fases α-AlFeSi aumentando el contenido de Mn, Cr y V en la aleación:
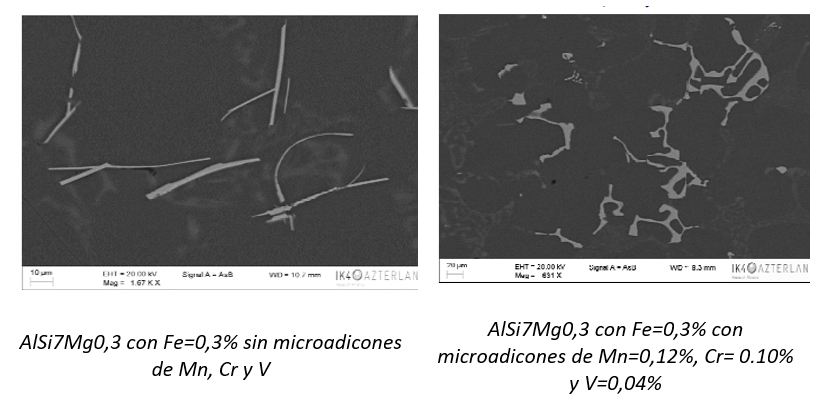
Figura 2. Transformación de fases intermetálicas ß-Al5FeSi a fases α-AlFeSi para un mismo contenido de Fe de 0,3%
Con la adición de Mn y/o Cr hay que tener en cuenta el riesgo de formar compuestos intermetálicos Sludge muy duros. Para evitar y prevenir la formación de estos compuestos intermetálicos, es fundamental tener en cuenta la fórmula Sludge Factor (SF= %Fe + 2x %Mn+ 3 x Cr%). Para un valor de SF=1,8, la temperatura del metal debe ser siempre superior a 650⁰C.