Importancia del conocimiento metalúrgico en la interpretación mediante la técnica SEM
En las últimas décadas, la microscopía electrónica de barrido (SEM) ha pasado de ser una técnica reservada únicamente a especialistas con alta cualificación en universidades y centros de investigación importantes, a convertirse en una herramienta habitual no sólo en todos los centros de investigación metalúrgica sino que también en muchos departamentos de calidad y/o divisiones de I+D de empresas de cierto tamaño.
La versatilidad de este tipo de equipos reside en la combinación de las capacidades analíticas propias de la microscopía electrónica -básicamente elevadas resoluciones con alta profundidad de campo-, y del microanalizador de energías dispersivas de rayos X (EDS), que casi sin excepción, se instala en todos los equipos de microscopía electrónica de barrido y que permite la caracterización química de partículas microscópicas. Esta combinación convierte a este tipo de equipos en una herramienta imprescindible para todo tipo de estudios relacionados con la caracterización metalúrgica, defectología y análisis de fallo.
Pese a ser equipos conceptualmente muy complejos, su manejo es relativamente sencillo, por lo que es posible formar a usuarios que en un corto periodo de tiempo son capaces de desenvolverse con soltura. Aunque son capaces de obtener imágenes de calidad y conocer diferentes opciones del microanálisis, en la mayoría de los casos, no dominan los fundamentos de estas técnicas, ni poseen experiencia suficiente para una correcta interpretación de resultados.
En el presente artículo reflejaremos dos errores frecuentes que hemos detectado en varias ocasiones y en base a los que se habían planteado rechazos y cargos. A nuestro entender, estos ejemplos no son sino el reflejo de las carencias que en muchos casos existen, no en el manejo del equipo, sino en la interpretación de los resultados.
1.- Análisis de fracturas en componentes de fundición grafítica esferoidal.
La observación de dos áreas diferenciadas en las superficies de fractura puede ser indicativa de la existencia de defectos de fundición, como microrrechupes o inclusiones, si bien no necesariamente es siempre esa la causa. En roturas a tracción de materiales de fundición esferoidal con matriz ferritico-perlitica, es frecuente que se genere una primera zona de incubación de la fractura de carácter dúctil. Cuando esta alcanza el tamaño crítico, se produce el colapso de la sección restante con un mecanismo de rotura súbito tipo cleavage. Lógicamente, en la zona dúctil el mecanismo de incubación es de tipo microcoalescencia de vacíos y los grafitos se convierten en puntos de nucleación preferente. Lo que ofrece un resultado donde el contenido de grafitos es aparentemente muy superior al que podemos encontrar en las zonas cleavage, en este área, la progresión de la rotura no se ve tan condicionada por la presencia de grafitos.
En el departamento de calidad de una empresa de montaje de componentes de automoción, se observó esta diferencia de densidad grafítica. Se confirmó además con análisis EDS, en los que se demostró que el contenido de carbono de la zona dúctil era muy superior al resto de la sección y al valor teórico -cuidado con las determinaciones de carbono mediante análisis EDS-. La interpretación no albergaba duda alguna. Se trataba de un defecto de fundición que se manifestaba en forma de zonas con mayor densidad grafítica, lo que era la causa de la presencia de dos áreas con mecanismos de rotura diferenciados – no una consecuencia de la existencia de ambos mecanismos-.
Como resultado, se tuvieron que seccionar y acondicionar metalográficamente muchas piezas, buscando estas zonas de mayor densidad grafítica, que en ningún caso se evidenciaban en las secciones preparadas. Se fue entonces un pasito adelante en la dirección equivocada y se identificó el defecto como “alineaciónes de grafitos” de carácter local y aleatorio, con lo que únicamente se podía evidenciar en las propias roturas. En resumidas cuentas, se hizo dar muchas vueltas al fundidor antes de aceptar la realidad, que no era otra que a las piezas no les pasaba nada y todo había sido un problema de interpretación.
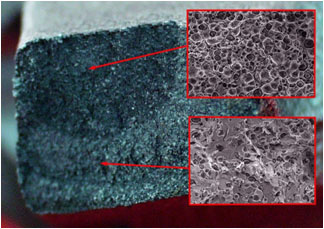
2.- Inclusiones en aceros laminados.
En los materiales laminados, especialmente si son de alto contenido de inclusiones, se produce un hecho similar al referido anteriormente, ya que las roturas dúctiles se nuclean preferentemente en torno a las inclusiones. Por ello, en fracturas longitudinales, se generan superficies de rotura de morfología fibrosa o leñosa, condicionada por la distribución longitudinal de las inclusiones. Como resultado, el contenido inclusionario aparente en la superficie de fractura es muy superior al que cabría esperar en una superficie metalográfica. Evidentemente, si se realiza un análisis EDS sobre la superficie de rotura, se constata el incremento del contenido de azufre que puede interpretarse como segregaciones o una alineación de inclusiones muy marcada. Es lo que ocurrió en una ocasión que tuvimos que defender una reclamación basada en que el contenido de azufre, determinado mediante el microanalizador EDS sobre una superficie de fractura, era muy superior al límite admitido por la norma para esa calidad. De nuevo en este caso, cuando se realizaban las probetas metalográficas correspondientes, el contenido inclusionario era correcto; ¡el fenómeno solo se evidenciaba en la superficie de fractura!.
Son dos ejemplos sencillos, pero a nuestro entender realistas del peligro de interpretar únicamente los resultados de la microscopía electrónica sin el dominio del análisis metalúrgico. En ambos casos, el error en la interpretación y la forma de actuar de la empresa cliente al imponer sus criterios, supuso grandes pérdidas en esfuerzo y coste económico.
