The international consortium of the CAESAR project, to which the AZTERLAN Metallurgical Research Center belongs, aims at improving the quality of low-quality scrap currently deposited in landfill and/or exported outside Europe. To this end, it will study and optimize processes of separation and elimination of impurities from this industrial waste, both through the development of new technologies and the updating of existing ones but that currently are not applied for the recycling of ferrous scrap. The project seeks to find new sources of raw materials for steelmaking sector that will allow to replace very high-quality scrap and pig iron.
Currently near 22 Mt of ferrous scrap from the steel manufacturing process is exported annually from the European Union to other countries while about 100 Mt of raw iron ore are imported.
However, in line with the steel industry’s growing commitment to improving its environmental impact and sustainability, the valorization of scrap (that is now discarded) through the definition of appropriate cleaning and sorting processes offers important opportunities for improvement and reduction of the carbon footprint.
As explained by AZTERLAN researcher Lucía Unamunzaga, coordinator of the Environment and Sustainability research line of the BRTA Member Center, “the question we were asking ourselves is why all this material, discarded or sold to third parties, is not reused to avoid the strong dependence of foreign markets on the supply of raw materials”. There are very advanced technologies with a high degree of maturity, whose proper combination and use present high opportunities to recover local scrap and reduce the import of raw materials, in addition to other important benefits, both went it comes to sustainability and at a competitive level.
In fact, the reuse of scrap is a common practice by the steel sector to improve the sustainability of the process. The production process for obtaining steel from scrap is based on its fusion in electric arc furnaces. This is a more energy- and environmentally efficient process than the one producing from iron ore. The manufacture of steel from scrap reduces energy consumption by almost 75%, raw materials by 90% and water consumption by 40%.
However, “among steel scrap we can differentiate two types: the so-called pre-consumer scrap, that is, the scrap generated in the steel manufacturing process and that is directly usable in the same process (represents 45% of the steel scrap), and post-consumer scrap, that is, the one generated in other industrial processes and which contains different types of impurities (inert materials, other metals, plastics …). The latter account for 55% of the available steel scrap”. The current trend is to keep reducing the amount of pre-consumer scrap, as a result of the development of more efficient manufacturing processes, while there is an increase in the second type of steel scrap, which, “unfortunately, does not have enough quality by itself to ensure the production of high-quality steel that European companies demand”.
In order to improve the recycling capacity of scrap, and especially post-consumer scrap, currently discarded, the CAESAR project was born. The project is formed by an international and multi-disciplinary consortium composed of research centers, technology development companies, metal recycling companies and steel manufacturers, and is focused on the development and validation of cleaning technologies that will enable to reduce impurities from post-consumer steel scrap and this material to be used in the manufacture of quality steel.
To achieve the objective set, the members of the CAESAR project will launch the following lines of work:
- Identification and characterization of new opportunities for the use and reuse of low-quality scrap
- Selection and integration of the most appropriate technologies to improve the quality of low-quality scrap, its classification and its characterization
- Industrial-level validation of a scrap sorting/cleaning demonstrator, based on an innovative combination of the most appropriate existing technologies
- Definition of recovery routes in the demonstrator for different scrap streams
In the words of Unamunzaga, “having a map of the characteristics of the different scraps that Europe currently is rejecting for steel production will be a fundamental initial step for the project”, since this “will allow us to identify the main residual streams and the most appropriate routes for their local recovery”. In the same way, the work team will select and integrate different cutting, crushing, sorting and cleaning technologies that ensure the separation of mineral and non-ferrous fractions, as well as the elimination of trace elements and impurities that could negatively affect the quality of the material and the final products.
Among the technologies to be used and integrated some already available on the market can be found. This is the case of ScrapTuning (Sicon), LaserSort (Sicon), Aspratel (Azterlan), LiDar (ArcelorMittal) or LIBS (ArcelorMittal). There are also different demonstrators, crushing technologies, classification technologies, vision and hiperespectral camera technologies, etc. that have been developed by the different entities belongint to the consortium. All these technologies will “in all cases be optimized for their industrial application and / or they will be adapted for the recovery of steel or to the specific characteristics of the metal”.
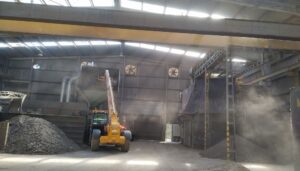
Facilities of the ASPRATEL company, dedicated to the recovery of metals
Finally, the different sub-wastes obtained from the steel recovery processes will also be subject of valorisation by the project members: “this may involve the recovery of elements such as, for example, aluminum or copper, among others. However, this step will depend on the type of non-ferrous elements contained in the scrap, as well as their recoverability after undegoing the various cleaning processes.
The expected result of the CAESAR project will be the generation of recovery routes for the main post-consumer scrap and all separate non-ferrous fractions, establishing a recovery target above 98% for the ferrous fraction of the scrap.
The CAESAR project consortium is participated by Centre de Recherches Métallurgiques, ArcelorMittal Basque Country Research Centre, ArcelorMittal Maizières Research, Rolanfer Recyclage, Reydesa Recycling, INATEC, SICON GmbH, ArcelorMittal Belgium, AZTERLAN Metallurgy Research Centre, Katholieke Universiteit Leuven, ArcelorMittal Sestao and ArcelorMittal France. The project is funded by Horizon Europe programme of the EU under Grant Agreement 101058520.