The ReIMAGIN consortium will delve into the hybridization of manufacturing technologies for highly competitive sectors such as the automotive, aeronautics, energy and machine tool sectors.
The evolution of manufacturing technologies and design tools allow the application of new materials in the manufacture of components of greater complexity and sophistication, favoring the development of new multi-material and multi-functional design and manufacturing practices.
Traditional manufacturing processes (such as casting, forging, stamping, HIP and their different forms of joining) have a high level of complexity and yet are still widely used for the manufacture of metal components. Additive manufacturing has been added to these processes, with increasing weight, since it presents important advantages in terms of the possibility of developing new lightweight designs, product customization, repair or integration of functionalities.
Following the successful collaboration within previous research efforts, the ReIMAGIN project team will continue to delve into the work of hybridization of manufacturing technologies, taking advantage of the multiple advantages of each of them, together with those of additive manufacturing. With this they seek to provide solutions for specific applications of great interest to highly competitive sectors, such as automotive, aeronautics, energy and machine tools, in various strategic lines of work such as weight reduction, improvement of electrical conductivity, heat conduction, corrosion resistance, impact or wear resistance, among others.
As Dr. Ana Fernández, a researcher at AZTERLAN, points out, “within the IMAGINE project we have already managed to demonstrate that it is possible to manufacture single-material components from the hybridization of two different technologies, without the joining points between the areas manufactured with the different technologies being the weak or critical points of the component. We were also able to observe that through the hybridization of these technologies we achieved components with the same metallurgical properties in both segments. Therefore, when we defined the research agenda of this new and ambitious work proposal, we started from an extraordinarily solid base, on which to continue building and innovating.”
In this way, among the new objectives that the work team pursues, some stand out: the design of new materials with ad-hoc compositions in the form of atomized powders, the development of multi-material components through additive technologies (LMD, EHLA), the optimization of welding processes for “special” materials (FSW, WAAM, solid bonding), or the development of heat treatments for parts manufactured using hybridized technologies.
In addition, ReIMAGIN also seeks to integrate new challenges such as digitalization and the sustainability of processes. “On the one hand, we want to increase digitalization in hybrid processes developed based on new simulation models of functional behavior, or microstructure prediction. At the same time, we will also work on the development of specific actions aimed at facilitating the retention of product value, its recycling and its environmental impact, as well as the energy efficiency of the process.”
The ReIMAGIN consortium is made up of 8 partners, the AZTERLAN, CEIT, LORTEK and TEKNIKER Technology Centers, members of BRTA; the UPV/EHU, MU universities; and the R&D business units FCIE and EIPC. All of them have complementary capabilities and benchmarks in the field of advanced manufacturing in the Basque Country in metallic transformation processes and products. ReIMAGIN is funded by the Elkartek program of the Basque Government.
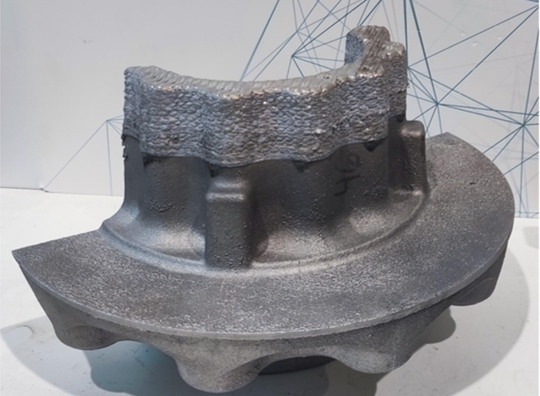
Mono-material component developed using hybrid technologies (HydroSolidification + Additive manufacturing) developed within IMAGINE project.