The recent conference on “Technical Cleaning Tests” organized jointly by LEICA and AZTERLAN, with the participation of NEURTEK and with the support of the TABIRA Foundry Institute, has allowed to delve into some key aspects of this analytical method of great value for the automotive industry. During the session the topics covered ranged from the regulations associated with this tests to the technologies and methodologies applicable for their realization. When it comes to AZTERLAN’s participation, Ana Barrena, a chemical analysis technician and an expert in technical cleanliness tests, presented the main keys of this test.
The aim of the Components’ Technical Cleaning Test is to determine the contamination of particles present in the most relevant areas of automotive components or parts and thus be able to prevent potentially dangerous particles from entering critical operating systems (such as hydraulic systems, engine…) to avoid in-service failures. This is a high-value, standardized test for the cars manufacturing industry with an increasing demand among OEMs who establish pollution limits and/or characteristics of dirt particles that are allowed to be present in the components. In recent years, demand has also been growing in other sectors such as aeronautics or orthodontic medicine, among other. The AZTERLAN Metallurgy Research Centre offers this test as a part of its analytical portfolio (accredited by ENAC according to ISO16232).
As explained by AZTERLAN chemical analyst Ana Barrena, “the concept of the procedure to follow during this analysis is simple: the component to be analyzed is washed with a specific fluid that is collected and filtered after the process to, finally, analyze the particles retained in said filter to assess the number, the size and the nature of particles; also a gravimetric assessment of the mass of contaminant is performed”. However, depending on the type of component to be analyzed and the requirements established by the OEM/client, there are multiple variables that must be taken into account for the correct execution of the study, such as “the definition of the parameters of the dirt extraction method from the part/s and the validation of such method through the declining test”.
In relation to these aspects, Barrena explained that the 2018 update of the ISO16232 standard “defines crucial aspects of the process in more detail than the previous version from 2007, including more detailed instructions for the validation process of the washing parameters. It also incorporates proposals for the parameters of the starting wash according to the chosen method, sets the parameters for the optical analysis by means of the microscope, exposes other verifications of the process such as the double check, specifies other size ranges for the study of particles, and also exposes handling instructions for the parts, packaging, transportation, etc.”
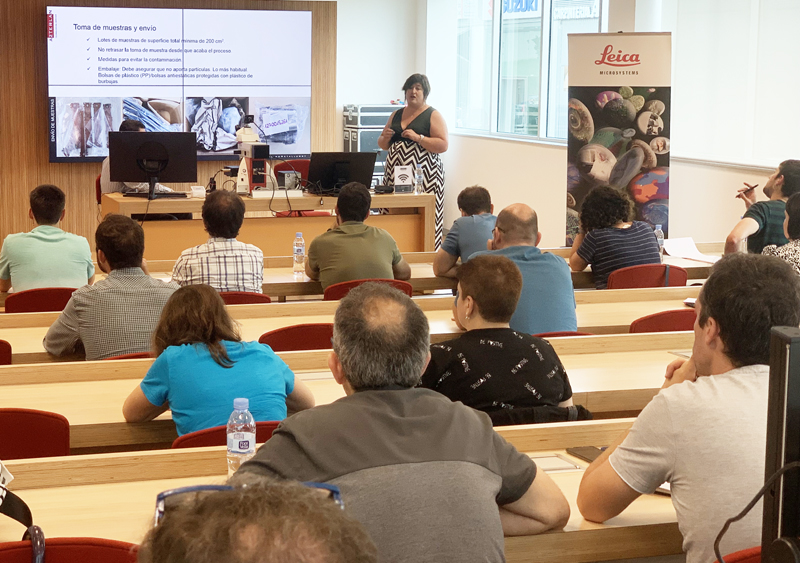
AZTERLAN Cleanliness Testing extepert, Ana Barrena, during her participation at the workshop
Definition and validation of the dirt extraction method
Although there are different ways to extract pollution from parts, the most common are the ultrasonic method and pressure washing. “In the first of them, the components are immersed in a fluid and are sonicated for a period of time to favor the detachment of the particles retained in them. In the second one, the products are rinsed with pressured fluid under specific conditions. Generally, the ultrasonic method is indicated for batches of small parts and the inspection of external and internal geometries while the pressure washing method can also be applied to larger parts and to inspect external and internal geometries that can be easily reached. The ultrasonic technique is very effective but it requires taking into account that the washing conditions are more aggressive, so it is not a suitable technique for all types of materials (for example, iron and aluminum castings, painted or coated parts, sintered components, etc.).”
However, a “fundamental aspect to ensure the reliability of the results is the validation of the extraction method itself.” With this orientation, Barrena explained the functionality of the “declining test” defined by the ISO16232 standard and that requires the performance of six consecutive extraction cycles under the same conditions to verify at what point a reduction greater than or equal to 90% of dirt is achieved, assessing in each cycle the mass of contaminant and/or number of particles. Once this criterion is reached, the washing conditions are extrapolated in order to carry out the test. “The objective is none other than to demonstrate that, indeed, we are extracting the retained dirt. If the process is done properlly, it will be possible to observe that the amount of dirt retained in the components is less and less in each cycle, obtaining a descending graph (also known as “decay curve”). A clearly descending trend will lead to consider that the extraction method applied it is valid. If not, the process should be readjusted.”
Other key aspects for a correct execution of the component cleanliness test
Along with the selection and validation of the testing method, the AZTERLAN expert revealed other important aspects to carry out the test and ensure the reliability of the results:
- Characteristics of the samples: The samples must have a minimum total surface area of 200 cm2.
- Test must be carried out in facilities and conditions that ensure that there is no cross contamination: In the case of AZTERLAN, the center has a cabin specifically designed to perform for this type of tests, which is located in a room equipped with air extraction and atmosphere separation systems so the entry of particles is prevented.
- Packaging and shipping of samples: The way in which the samples are sent to the reference laboratory for analysis must ensure that no particles are added during the different processes associated with the packaging and shipping of the samples.
- Analysis supported by software: Although the analysis of the particles retained in the filter can be carried out by visual inspection and manual counting techniques, the analysis supported by specific software offers speed and reliability to the results. In the case of AZTERLAN, since 2014 the center works with a LEICA DM4000 M LED microscope with specific software Leica Cleanliness expert 4.5.0.
To evaluate the results, gravimetric evaluation (for which, after the filter has dried, it is weighed to determine the mass of contaminant) and an assessment of the retained particles, mainly determining the number and size of the particles, as well as their nature, are combined. “To perform this last analysis, at Azterlan we use a microscope with crossed polarizers to be able to distinguish bright and non-bright particles. Thanks to the image analysis software, the size ranges of interest are defined for the system to carry out the counting and quantitative evaluation”.
In this sense, since it is “a poweful tool that provides interesting information of a qualitative nature” Barrena indicated that, on certain occasions, it is also interesting to complement this analysis with “an analysis using scanning electron microscopy (SEM), especially if there are doubts about the provenance of a certain pollution or if we are looking for introducing adjustments in the production, processing or logistics processes associated with the analyzed parts”.
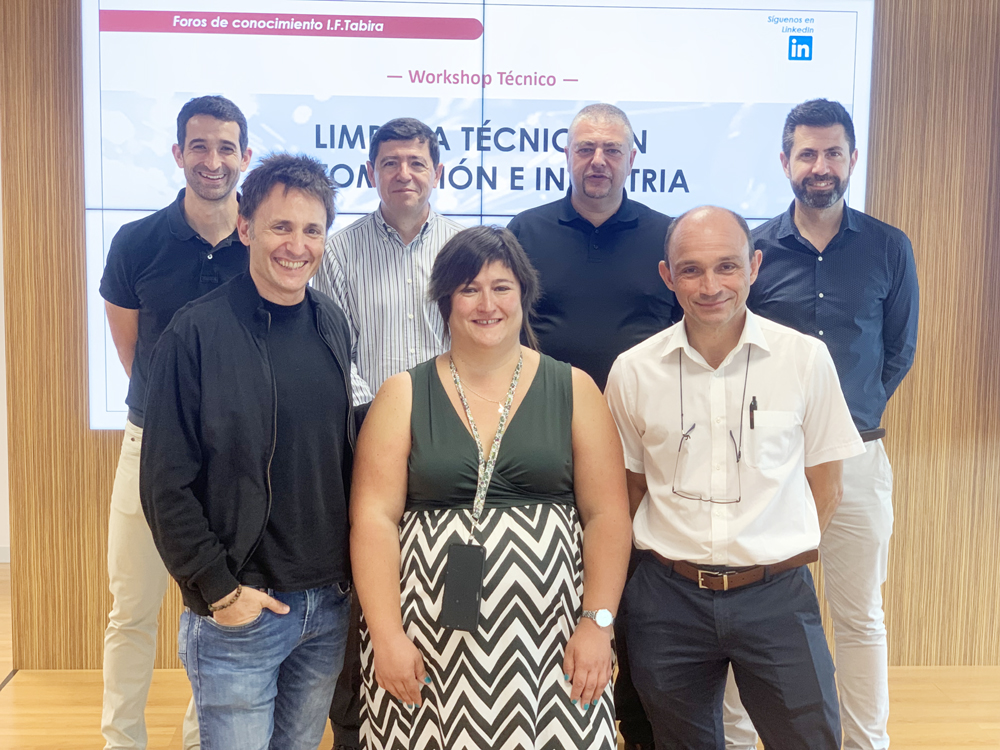
Representatives of AZTERLAN, Leica, Neurtek and Tabira Foundry Institute.