The 8th edition of the “CH2 – International Conference on Hot Sheet Metal Forming of High-Performance Steel” has been held in Barcelona from 30 May to 2 June. In the same, the research team of Forming Technologies of AZTERLAN has presented two works related to the forming of aluminum-lithium alloys to manufacture aeronautical components and the coefficient of heat transmission in hot-formed 6xxx series aluminum alloys.
The work “Formability study of 2198 aluminium alloy for hot stamping” has been presented by PhD. Maider Muro, AZTERLAN researcher, who has shared the main outcomes of the study carried out to validate the conformability of the light alloy 2198-T8 Al-Li, widely used to manufacture aircraft components, by means of hot stamping technology. “Hot stamping is a transformation technology widely used by the automotive sector for the forming of steel parts. However, to transfer this technology to the aeronautical sector (with a much lower production rate) and, more specifically, to the forming of new materials, such as lithium-aluminum alloys whose behavior to these manufacturing conditions it is unknown, the corresponding feasibility studies must be performed beforehand to define the appropriate manufacturing conditions, both from the metallurgical and process point of view”.
The work presented by PhD. Muro is based on the research work developed along with BATZ S. Coop. within the Rib-ON project (see video), by using FLD (Forming Limit Diagrams) at 450ºC, “the recommended temperature by the manufacturer of the material”, and at 200ºC, “which is considered as the minimum forming temperature for aluminum sheets of these characteristics, a thickness of 1.8mm”.
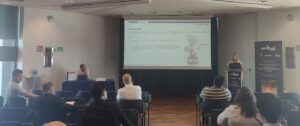
PhD. Maider Muro presents the work “Formability study of 2198 aluminium alloy for hot stamping” developed together with Batz S. Coop.
On the other hand, the second work presented by AZTERLAN under the title “On the effect of testing setups on aluminum alloys Interfacial Heat Transfer Coefficient Measurement” in collaboration with the University of Mondragon (MU), has focused on the determination of the Heat Transmission Coefficient of aluminum in hot stamping. “This concept is closely linked to the cooling speed in hot stamping, and it is conditioned by aspects such as the surface of the dies, the geometry of the sheet to be stamped, the contact pressure between both elements and the temperature differences between them”.
The research work presented has shared the study carried out in parallel in two independent laboratories (one of them AZTERLAN facilities) in order to measure this coefficient between a 6111 aluminum alloy and a forming tool made of a QRO90 tool steel at three different working pressures (1 MPa, 5 MPa and 10 Mpa). “Experimental works like this one are necessary for the development of models regarding the behavior of materials, fundamental for the design of new components and new manufacturing pathways.”Among the conclusions presented, the work team has emphasized the “need to improve the means for capturing and transmitting critical process data that occur in spaces of difficult access (such as the contact areas between the materials to be formed and the forming tools)”, indeed, this is a main field of work in which the research team is focused within the SUSIE project.
The works presented by AZTERLAN at this congress are the result of the projects RIB-ON (funded by the Clean Sky 2 joint udertaking within the Horizon 2020 program of the European Union with license number 755493, and SUSIE (Disruptive Surface Sensor Integration), funded by the Basque Government through the Elkartek programme (KK-2020/00063).