AZTERLAN and MESHIND, in collaboration with MGEP, have demonstrated the feasibility of manufacturing forged fasteners using as-clad bi-material bars as raw material.
The main advantage of developing protective surfaces through additive technologies is the possibility of manufacturing multi-material components in which the main body of the part (substrate) is composed of a “common” material responsible for fulfilling the structural function (mechanical loads), while a surface made of an advanced material provides the component with improved resistance to phenomena such as corrosion or wear.
In this manufacturing strategy, the usual procedure consists of first shaping the main body of the component (through casting, stamping, forging, or another process) and then applying a protective layer to its surface by adding ad-hoc metal powders by means of laser technologies. However, this combination of technologies presents some limitations, mainly related to the reduced scalability of the process. As explained by AZTERLAN researcher Dr. Ana Fernández, “coating already shaped parts by means of LMD technologies one by one is not an easy process to implement at certain production rates and amounts of products.”
In order to take advantage of the benefits offered by bimaterial manufacturing for the development of critical components and seeking to optimize their manufacturing process, AZTERLAN, a technology center specialized in metallurgy, and MESHIND, a company specializing in the development of industrial solutions based on additive technologies, have developed an innovative hybridization strategy for forging and LMD processes based on the application of advanced coatings directly on the raw material, prior to the forging process.
Development of forged fasteners from an as-clad material
After conducting several tests combining different parameters for the cladding and forging processes (varying temperatures and geometries), as well as evaluating the effect of subsequent heat treatments, the research team successfully manufactured fasteners with a 42CrMo4 steel body and an advanced AISI 316 stainless steel surface using LMD coat base-material bars with a 1 mm thick layer of stainless steel. This bi-material was subsequently forged to get the aimed faster shape.
The standardized corrosion and hardness tests perfromed on these components demonstrate that this is a valid approach for developing bi-material components with improved corrosion resistance. “The advantages offered by this methodology are clear: Not only does it ensure the performance of the parts in corrosive environments, but it also achieves significant savings in terms of processing time and finishing machining operations.”
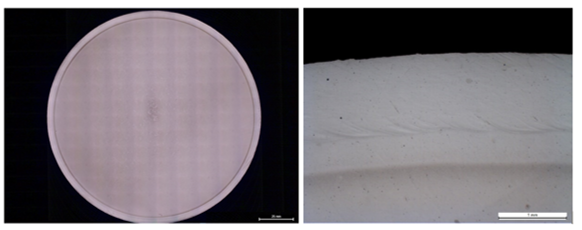
Cross-section and side view of the as-clad cylinder viewed through a magnifying glass (left) and optical microscopy (right), showing the substrate and coating.
Successful hybridization of manufacturing technologies.
This research was carried out within the ReIMAGIN project, aimed at providing solutions for specific applications of great interest to highly competitive sectors through the design of new materials with ad-hoc compositions in the form of atomized metal-powder, the development of multi-material components using additive technologies (LMD, EHLA), the optimization of welding processes for “special” materials (FSW, WAAM, solid bonding), and the development of heat treatments for parts manufactured using hybrid technologies.
The ReIMAGIN consortium is participated by eight partners: the technology centers members of BRTA AZTERLAN (project leader), CEIT, LORTEK, and TEKNIKER; the UPV/EHU and MU universities; and the R&D business units FCIE and EIPC companies.