The Druckgusstag conference was held at the reference Euroguss trade fair dedicated to aluminum injection technologies. In this outstanding international technical meeting AZTERLAN has presented the Alu-V® technology to be applied in HPDC along with two advanced experiences on the use of additive technologies for the advanced integration of sensors in injection molds.
In the first of the presentation, the AZTERLAN Light Materials researcher Sergio Orden has unveiled one of the most innovative developments of the Center for High Pressure Die Casting: the Alu-V® technology, a system to generate low-medium vacuum and Alu-V+, for high vacuum generation. “Porosities caused by the air retained in the molds are an inherent problem in the High Pressure Die Casting (HPDC) manufacturing technology. When the molten metal is injected at such a high speed into the mold, the air in the cavity does not have enough outlets to get out and part of it gets trapped in the metal, generating gas porosity. With the development of Alu-V® (and Alu-V+) technology we wanted to reduce this problem and ensure higher quality injected aluminum components”. Although there are already some vacuum generation systems available in the market, “these other solutions have important limitations given their tendency to generate a sucking effect that causes an inconsistent filling pattern of the molds”, affecting negatively the quality of the molten parts.
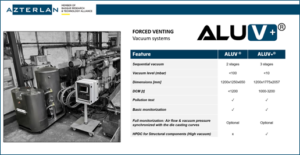
Alu-V Druckgusstag presentation
As explained by Mr. Orden, “vacuum generation by means of this new development presents significant opportunities to HPDC manufacturing, such as the development of components with thinner walls or ensuring the weldability or thermal treatability of parts”; likewise, “we have created Alu-V+ (high vacuum) in order to facilitate and to improve the manufacturing capabilities for structural components”.
The representative of AZTERLAN remarked in his presentation the importance of 4.0 industry technologies and the monitoring of key parameters of the process to ensure its effectiveness and the quality of the result. In this matter he stated that “when developing the Alu-V® technology we have taken into account the growing process control requirements of the High Pressure Die Casting technology, so we ensure that our equipment are able to capture and emit key data, such as pressure, humidity and airflow, all of them synchronized with the rest of the variables of the injection process”.
On the other hand, centering his work in the opportunities that additive manufacturing technologies present for HPDC, AZTERLAN researcher Emili Barbarias, specialized in Aluminum and Light Materials transformation technologies shared two successful experiences linked to the optimization and monitoring of this process developed along with the companies VOESTALPINE and ELECTRONICS GmbH.
The first of the experiences shared by Mr. Barbarias consists of an innovative distributor located in the HPDC cold room manufactured by means of additive technologies, whose implementation has allowed “to reduce the cycle time by 3 seconds in comparison to conventional distributors. The main reason behind this achievement is a significant improvement in its ability to dissipate heat”. As explained by Emili, this experience has been accompanied by the integration of several sensors (thermocouples and a temperature sensors of the cavity and directly in contact with the metal) that has allowed the team to monitor the key variables and to determine the success of the invention.
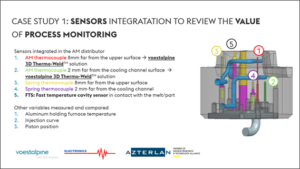
Additive manufacturing insert in HPDC
As a second successful experience that the multidisciplinary working team brought to the Druckgusstag, the AZTERLAN researcher presented an optimized redesign of the cooling channels targeting the improvement of the useful life of a sensorized insert that was also manufactured using additive technologies. “It is a key insert that offers relevant data related to the shrinkage and die-soldering phenomena. However, it suffered a rapid deterioration due to the thermal stresses suffered. The aim of the improvement presented was to prolong its useful life in addition to ensuring the stability of the process regarding the incidents in the mold and the quality of the product. We are currently collecting a lot of critical process data that will provide us with important information and knowledge in the future”. In HPDC production, “the important phenomena we want to observe usually occur in areas of the manufacturing process that are hard to access (like inside the molds) and where working conditions are harsh, affecting the durability of transducers and data loggers. Because of that, part of our 4.0 industry research effort is aimed at ensuring that critical process parameters can be captured and that the pathways by which we can achieve them are consistent, reliable, and stable”.