The new infrastructure, which will be part of the Technology Center’s Advanced Technologies Unit, will allow AZTERLAN to strengthen its R&D offer for foundries, as well as its capabilities in the field of development of experimental prototypes of complex designs and new materials. This infrastructure is complemented by other capabilities of the Center dedicated to the characterization of sands, to the development of new strategies for manufacturing sand molds and to the fusion of metallic materials.
3D sand printing presents significant advantages related to design flexibility, making it possible creating molds and/or cores with extremely complex geometries and eliminating the need to have physical models of the different sections of the components to form the shape of the mold/core. In this additive technology, the liquid resin is applied selectively on a thin layer of sand (that has been previously activated), carrying out a layer by layer deposition by injecting the reactive resin in the areas previouslly defined by CAD. This is an important field of work to continue advancing in the development of new designs of complex components, innovative feeding and filling systems or in the traceability and digitalization of molding and solidification processes, among others.
The new scientific-technological infrastructure for the development of molds and sand cores will reinforce AZTERLAN’s R&D work through the manufacture of innovative molds and, with them, advanced metallic components with greater functionality and performance, helping AZTERLAN expand their knowledge and enhance their capabilities when it comes to the design and development of new solutions. These new capabilities will also provide a significant support to AZTERLAN’s prototyping activity focused on the manufacturing of experimental prototypes of novel designs and special materials, providing greater flexibility and agility to the Center’s research teams.
These new capabilities will expand AZTERLAN’s offer of innovative solutions for molds additive manufacturing sector and castings manufacturing industry, as well as for different client sectors, like the automotive sector (including combustion engines and E- mobility), hydraulic parts manufacturing sector, aerospace sector and to the recycling and reuse of foundry sands.
Among the research lines that AZTERLAN will be able to stenghten thanks to this new infrastructure the following can be highlighted:
- Design and manufacture of parts with very complex geometries (shapes not achievable by traditional manufacturing systems) by casting in sand molds/cores
- Design and manufacture of lightweight components and/or with bio-inspired and/or reticular concepts by casting technolgies
- Design and manufacture of cast parts capable of replacing sets that are currently assembled
- Manufacture of molds for the insertion of all types of sensors with the objective of monitoring in real time the filling process, solidification, deformation of geometries, flatness, gas generation, etc. of the castings
- Building defect prediction systems related to the filling and feeding process of cast parts, as well as those coming from the generation of gases inside the mold
- New strategies for positioning componets in the molds to optimize mold/metal performance and reduce energy and material consumption, as well as minimize deformation defects and thereby reduce machining needs by bringing the dimensions of the cast parts closer to the final geometries
- New strategies for casting filling systems that minimize widespread problems related with inclusions
- New feeding system strategies that reduce the size of the risers and increase yield
- Manufacturing strategies for producing castings with built-in cooling systems
- Manufacturing strategies to control the cooling rate (“engineered cooling”) of castings with the aim of achieving optimized mechanical properties
- Strategies for reusing spent sand, thereby reducing landfill waste disposal, promoting circular economy, improving recyclability and reducing environmental impact
- Exploring the advantages of mixing additive and conventional manufacturing systems to achieve parts with geometries that do not yet exist
Fully equipped infrastructure, that is complementary with other advanced capabilities of AZTERLAN
This new capacity for manufacturing molds by means of additive technology will be set in fully equipped facilities that will house, among others, a 3D sand printing machine, sand mixing, shifting and supplying systems and molds curing, unpacking, cleaning and handling areas.
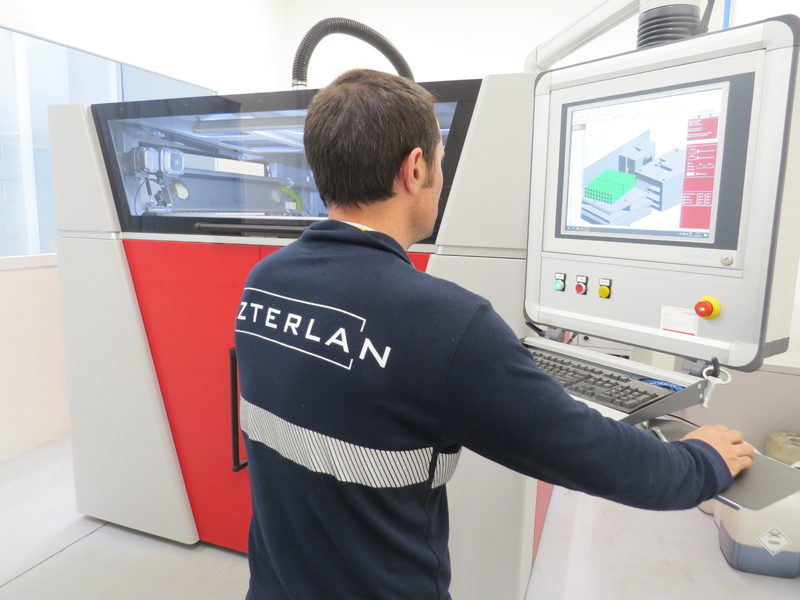
Sand 3D printing system: additive manufacturing of sand molds and cores
This new technological capacity is complemented by other advanced capabilities of AZTERLAN for the physical, chemical and mechanical characterization of sands, the fusion of metallic materials and the atomization of metallic powders. In addition, AZTERLAN has fully equipped characterization and testing laboratories to assess the properties of the manufactured parts.
This new infrastructure is partially financed by the Provincial Council of Bizkaia.