Lead by the IK4-AZTERLAN Metallurgy Research Centre and with the participation of an outstanding consortium of companies and entities, such as ACCIONA INFRAESTRUCTURAS, FUNDICIONES DEL ESTANDA, ONDARLAN and GAIKER-IK4 technology centre, the LIFE ECO-SANDFILL project has offered significant advances in the research performed to reuse waste foundry sand as a fine aggregate for diverse construction applications like ramparts, mortars and low controlled resistance materials.
Funded by the European LIFE 2015 program, under the title
“Spend foundry sand valorisation in the construction sector through the validation of high-performance applications”, the project aims at demonstrating the technical, environmental and financial viability of reusing spent moulding foundry sand within the foundry industry, as well as in further applications for the construction sector. For this last purpose, foundry sand must undergo a regeneration process based on the fluidized-bed attrition.Starting from the physical, chemical, mechanical and environmental requirements that the sand must fulfill to be used in aggregates for each specific application, the operating conditions of the regeneration system that make possible to obtain the best properties have been defined. The same conditions are also oriented to ensure a lower financial and environmental impact in comparison with the initial situation (deposition in landfills as waste).
For each application, numerous laboratory tests of regenerated sand dosing have been carried out with the aim of stablishing the maximum substitution conditions and percentages that guarantee the technical quality of the resulting products.
Ramparts and constituting materials
The characteristics of ramparts and constituting materials are governed by the specifications included in the General Technical Specifications for Road and Bridge Works (PG3).
The studies performed to the regenerated foundry sand show that they are suitable to be used in tolerable grounds in the nucleus and cementation zones of the rampart. Anyway, the morphological and granulometric characteristics of the regenerated foundry sand requires the mixture with borrow soils, so the compaction and stability of the nucleus of the rampart is not compromised. For this purpose, a maximum 80:20 ratio of foundry sand-borrow material has been settled.
Low controlled resistance materials
Regarding low resistance materials, the applications are aimed at compression resistances between 0.3 and 8 MPa, which offer a similar construction performance to those of stabilized grounds. These materials are conceived for non-structural applications such as ditch-filling in electric conductions, water piping, insulators, erosion controls, etc.
With a 100% substitution >2MPa resistances can be obtained. Therefore, they can be applied in a great variety of applications, in the amounts that satisfy the resistances or other quality requirements demanded by each construction work.
Mortar
When it comes to mortars and to the specifications that rule the properties of aggregates (UNE-EN 13139:2002: Aggregates for mortar), foundry sand can react to the alkalis of cement. Therefore, the percentages applied depend on the materials used in the mix, as well as the kind of mortar. Up to 50% substitution ratios can be reached in mortars of lower resistances.
Pilot experiences that evidence the viability of foundry sand in construction applications
With the aim of demonstrating and validating the use of spent foundry sand among construction materials in actual conditions, pilot experiences are being implemented. They will allow to study the properties and the performance of the materials designed over the time.
Specifically, as a part of the construction works of the new building of the IK4-AZTERLAN Technology Centre two different experiences have been carried out applying different mortar products. Both products are based on foundry sand as a replacement for other aggregates that come to improve the technical performance described by the mortars of reference.
One of them consists of a thermal mortar placed over the floor climatization system in the base level of the building (660 m2). This mortar is composed with a 5% of foundry sand and it keeps the mechanical and thermal properties of the mortar of reference but requires less water during application.
The second demonstration experience has used filling mortar on the external paving of the building (185 m2). The mortar has been manufactured with a 20% of foundry sand that substitutes natural sand with the same granulometry. This condition has allowed to improve by 40% the mechanical resistances presented by conventional mortars
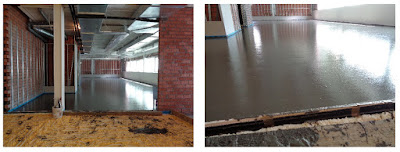 |
Application of a thermal mortar with foundry sand in the radiant floor system of the new facilities of IK4-AZTERLAN Metallurgy Research Centre. |
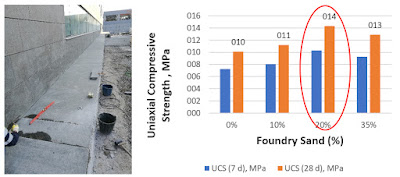 |
(Left) Application of a filling mortar based on a foundry sand formulation for the paving of the external area of the new facilities of IK4-AZTERLAN Metallurgy Research Centre. (Right) Mechanical properties of the mortars with different sand substitution percentages. |
Next materials for study
The next materials based on foundry sand being studied and still to be developed are non-structural concretes. Their technical conditions and specifications are ruled by the Spanish Regulation for Structural Concrete (EHE 08). The pilot demonstration of the developed material will be performed within the “Project to Build the New Emergency Exits of the High-Speed Vitoria-Bilbao-San Sebastián Line Tunnels. Section Bergara-Astigarraga”. These construction works are managed by Euskal Trenbide Sarea (ETS), the entity that collaborates with the project after an agreement signed in February 2019.
The use of this kind of residual sand in the construction sector has shown to be a valid and feasible alternative with enough capacity to absorb a significant part of waste foundry sands generated by the casting industry. These results encourage both the industry and the research community to keep working in the same direction, developing recycled high added value materials and demonstrators that allow an advanced and sustainable management of these kind of materials (bringing as well significant technical improvements in many cases).