Die-casting is a widely used manufacturing process for the production of aluminum components. Among its virtues, a remarkable one is the possibility to produce parts of complex geometry, with thin thicknesses, with a very good dimensional accuracy and with a high productivity. However, one of its drawbacks is that the soundness of the component is compromised due to the porosity, inherent to the process.
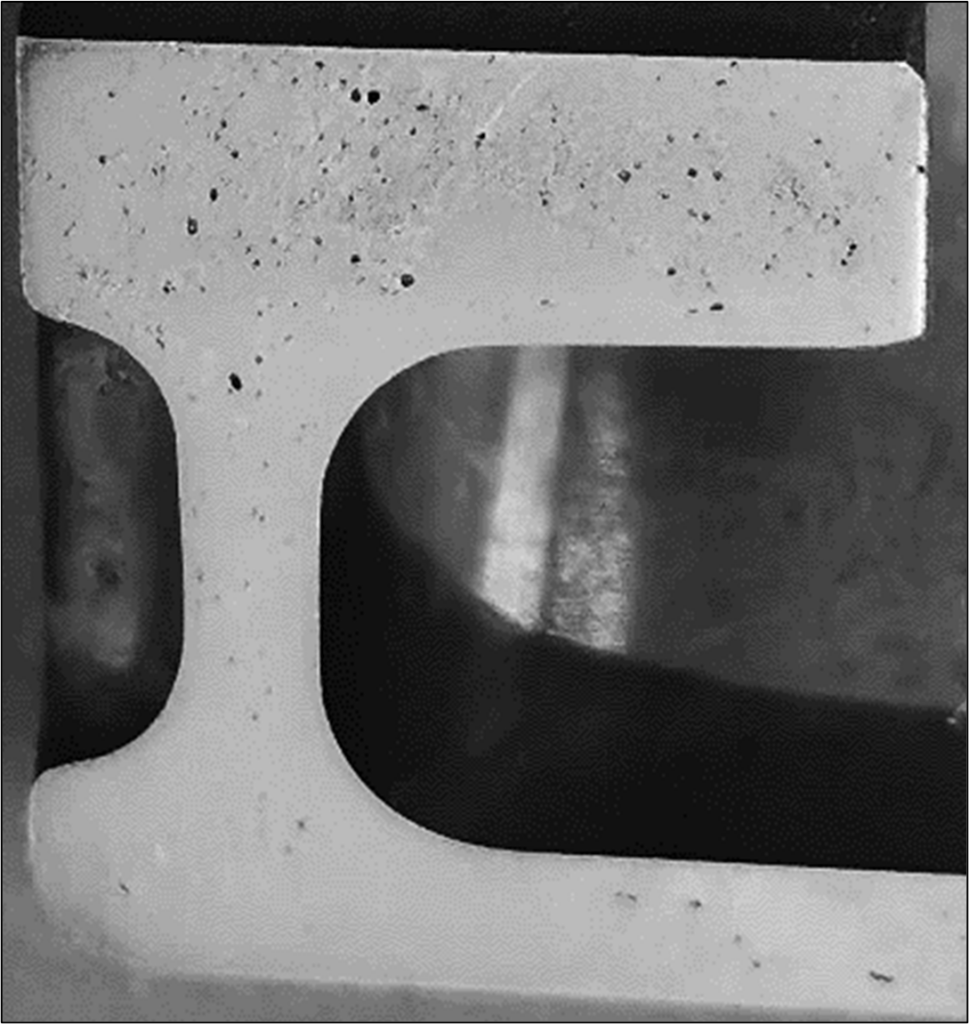
Image 1: Porosity in a cutting plane of a conventionally injected part
But why is there porosity in injected castings? It must be considered that in this manufacturing technology the molten metal is injected into the mold at high speeds and the cavity is filled in a very short time (approx. 0.1s). Ideally, to produce a part without porosity the metal should push all the gas out of the cavity and replace it with liquid metal. All this in just a few milliseconds, which makes it extremely complicated. In addition, it can happen that inside the cavity prior to filling there are other elements but air, possibly water and / or steam. Even though avoiding this means of manufacturing could seem to be the first option, a manufacturing process that makes it possible to get complex and small thick pieces would be lost.
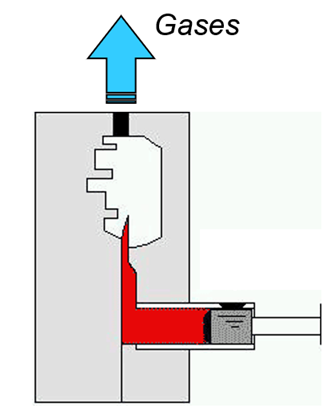
Image 2: Scheme of the conventional injection process
The process of supplying the molds with suitable gas outlets is very important to produce quality parts. To deal with the problem of air trapping, the cast aluminium sector currently has methods to allow the air to leave the mold cavity that could be classified into natural ventilation and forced ventilation.
In natural ventilation methods the air is pushed outside the mold by the metal during the filling of the cavity through grooves that allow the outlet of air, but not aluminum. The most basic form of groove is a flat machined space from the 0.1mm deep overflows. However, this type of ventilation is almost always insufficient. Another more efficient form of natural ventilation is the use of Chill-Vents. It is a solution with a much greater groove thickness (up to 1mm) but thanks to its sinuous profile it does not allow aluminum to come out. As a natural ventilation it allows a greater ventilation section but that can sometimes also be insufficient to minimize porosity to the maximum.
In forced ventilation methods, the process is equipped with a rapid evacuation of air through a system with a high vacuum tank connected to the mold in such a way that moments before filling the cavity the air inside is extracted to facilitate filling and avoid it to keep trapped. If the system is well designed, installed and programmed, parts with proper internal soundness can be obtained.
However, it is necessary to take into account the reality of leaks with these systems since to obtain an ideal vacuum in the cavity of the mold everything should be completely sealed from the tank to the piston. Otherwise, the vacuum in the cavity will not be the same as in the tank. Vacuum in the mold cannot be guaranteed, although there will be forced ventilation.
On the other hand, the use of this technology during the injection process implies a possible less known adverse effect: the disturbance of the metal front. This happens in current vacuum systems where a large tank with high vacuum is connected to the mold at atmospheric pressure instantaneously to achieve the desired vacuum level of the mold. It has been shown that the sudden application of a strong vacuum supposes a great suction force resulting in the breakage of the metal front with an inconsistent and not repetitive behavior of the filling of the mold, that is, the quality of the component will be below from expected.
The proposed solution is the combined vacuum technology developed by AZTERLAN with the ALU-V® system, which allows working with a vacuum system in which the limitations of current systems are overcome, achieving a step further in the quality of the injected castings.
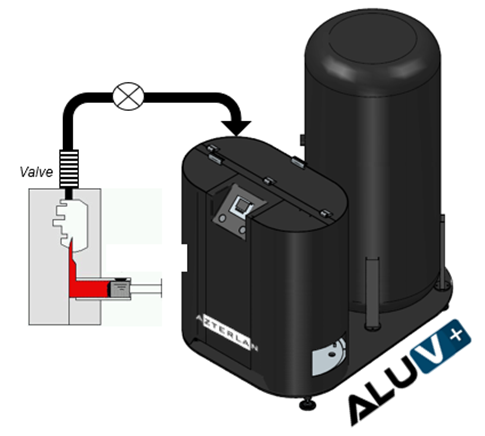
Figure3: ALU-V®+ System Schematization
Towards a 4.0 HPDC manufacturing
The control of any manufacturing process is essential to guarantee optimal results. Vacuum systems, in particular, require new process variables that must be monitored and controlled to ensure consistent results.
The ALU-V® system consists of vacuum pressure, suction air flow and humidity sensors from which critical process variables can be monitored at each injection, such as vacuum pressure just before cavity filling or the volume of air sucked from the closing of the container mouth to the filling of the mold. In addition, it makes it possible to monitor the variables related to the vacuum in a synchronized way with the movement of the piston, allowing to have a complete and unified control of the injection process.