After thousands of years among us, foundry still encloses many mysteries that might lead us to think that its behaviour is arbitrary and out of our control.
One of the most critical reasons that justifies this behaviour is based on the solidification process and the complexity shown by the Fe-C diagram in the formation of different phases such as graphite, austenite and carbides.
The presence of additional elements in the chemical composition such as Si, Mg, S, Mn, P, along with another set of trace elements, contribute to distort even more this theoretical behaviour. Indeed, factors like the cooling kinetics and the nucleation level of the molten metal increase the difficulty to predict the final results of this complex solidification process.
Based on these factors, different alloys with a similar chemical composition can solidify following any of the “infinite ranges” that exist between the stable and meta stable diagrams.
“Metallurgical knowledge, along with advanced metallurgical quality control tools, is key to optimize foundry processes”.
The precipitation of the graphitic phase is a key factor in this kind of materials, not only because of its influence in the mechanical properties, but also in order to manage the contraction/expansion balance of the different phases that are formed during solidification. These phases regulate the tendency of the metal to develop micro shrinkage defects.
Therefore, the control of the chemical composition is not enough to dominate this process and to predict the behaviour of the parts being manufactured.
Developments of AZTERLAN Metallurgy Research Centre to assure the quality of cast components
This lack of accuracy to predict the characteristics of the metal has led AZTERLAN Metallurgy Research Centre to develop an innovative metallurgical control tool based on thermal analysis called Thermolan®.
Thermolan® system allows to model the growth of solid phases along the solidification time, as well as to visualize the eutectoid transformations in the solid state on real operation time, which is a clear advantage to foundry technicians and operators.
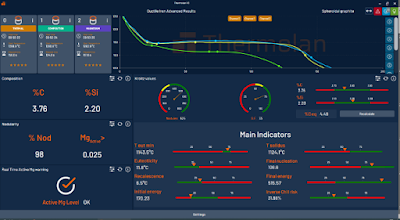 |
Monitoring screen of Thermolan® v 3.0 System. |
The cohabitation of such different phases like graphite and austenite, with densities differing more than 300%, substantially impacts the contraction/expansion balance.
Being able to control this balance becomes a competitive advantage because the control of the graphitic expansion helps to increase the self-feeding level, reducing or minimizing the need for external feeding.
Thermolan® facilitates the stabilization of the metallurgical process by means of measuring the impact of processes, materials and working procedures. At the same time, it incorporates predictive models based on algorithms designed by AZTERLAN to virtually anticipate which will be the key properties of the components to be manufactured.
The efficiency of the plate and mold design (being translated “efficiency” into plate yield: net /raw weight) is one of the aspects that strongly impacts production costs because it determines the use of energy and other materials. One of the clues for competitiveness is obtaining a high yield performance by minimizing the use of external feeders.
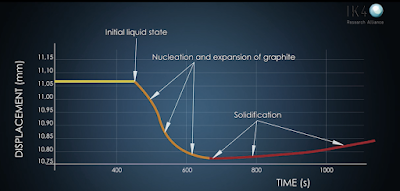 |
Representation of the development of the graphitic phase during the solidification process |
Dominating the graphite growth model has led AZTERLAN to turn this critical parameter into a mandatory input for a new foundry-targeted software development called “Kasandra”.
The Kasandra software developed by AZTERLAN integrates the thermal evolution of an alloy that is cooling inside a mold along with the calculation of the evolution of the solid fraction over time, considering as well the specific geometry of the component (thermal modulus).
The evolution of the solid fraction is the one that will condition the feeding demands of the parts and allows to predict shrinkage defects in real time. This innovative software is therefore a perfect supplement for Thermolan®.
The proper use of these techniques and tools brings a real paradigm change regarding the control of the casting process, as well as in the challenge linked to the design of the feeding systems, that were unimaginable until now.
The metallurgical knowledge and the wide expertise of AZTERLAN related to foundry technologies have allowed the Technology Centre to develop these advanced process control tools, which suppose a great technological step towards the optimization of the casting process and the competitiveness improvement of foundries.