Latest technology advances have been able to blend digital and physical worlds. Internet of things (IoT) is becoming prevalent in industry as it enables to connect all machines, products and systems involved in the manufacturing process. Filtering, evaluating and translating incoming data into meaningful information, on top of intelligent and autonomous decision-making software developments, steer to fully control and monitor the complete process. This means that people, machines and products can now communicate and interact with each other, reacting to unexpected changes in the production at real time and achieving a steady increase in performance.
Foundry industry is already far away from the ancient handicraft production and endeavours to catch the Cyber Physical Systems (CPS) drift. The digitalization of the immense masse of data generated, together with sensor controlled machines embedded in a network with ICT (Information and Communication Technologies) systems enables the interaction between devices and final soundness of the castings. The acquisition of appropriate process data and the use of artificial intelligence software provides the possibility to establish the best production conditions for any single casting, detect any parameter out of range and to correct any step of the process to guarantee that customer requirements are always fulfilled.
But going even beyond, the devices are self-optimized and self-configured, giving intelligent support to the process and adjusting it according to the specific needs at that very moment. This so-called “smart process”, where everything is under control, permits having strengthened and flexible processes that can be easily adapted to any casting, alloying product or process variation.
The deployment of advanced techniques to minimize machine deviations, along the use of newest well based design criteria, allow to reach the so called “smart product”, in which operations that do not provide any added value (fettling and finishing operations) have been removed, supplying to the customer a high quality casting of unbeatable aspect with the corresponding operational cost optimization.This is the basis of the foundry of the future.
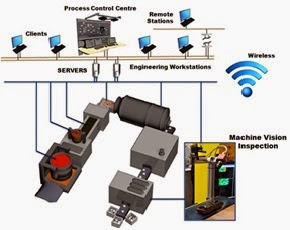
Intercommunication layout in a foundry process
IK4-Azterlan has developed a fully integrated system to succeed in this pathway. Its well known thermal analysis system (Thermolan) for the melt quality control, together with the latest own developments on artificial intelligence software (Salomon) which takes advantage from all the variables measured in the process, and the real time simulation prediction software (Eidocalc), which includes the melt quality at that very moment, allows achieving the most advanced “smart process”.
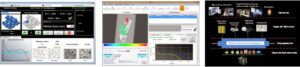
Advanced developments from IK4-Azterlan that allow to achieve a “smart process”
From another point of view, the expertise in design technologies to get optimized and self-breaking feeding systems and its proven experience in adjusting and controlling mould making devices within the foundry-shop allow to get a “smart product”, which are burr-free and self isolated castings from their feeding system. As only final inspection and packaging are needed, the lead time from raw materials to final product is reduced to 5 hours in foundries with automatic moulding lines. Besides, the best acknowledge from customers and profitability for the company is achieved.
This revolution is already a fact, but still needs to go further. “Smart process” and “smart product” developments have to be combined with a global Internet of Things. With billion devices and systems capable of communicating and consulting one with each other and without any human input, the entire value chain of a product in which a casting is involved is fully controlled across its whole service life. It will give the chance to react fast enough in order to satisfy market changes and customer requirements more closely.
But even more, it will generate data about failures, which conveniently analyzed will give information about how casting, machining, assembly, service in use, etc., can be improved to overcome new market requirements. This fact, which was beyond imagination a few years ago, will be a reality in the near future, in which final OEMs will need to face with this Big Data situation, while the rest of players will be required to a rapid adaptation of their processes to this working guideline, as it is the case of foundries.